Synopsis
The project Perforate stemmed from the RnD process of PDNB and aimed to extend the boundaries of concrete 3D printing. My responsibility was to investigate possible design options for wall panels that could be accomplished using concrete printing beyond the traditional 3-axis printing, deviating from the conventional approach of entirely layer-by-layer printing and solid structures.
Keeping the designs fully procedural was crucial as the goal was to develop a procedural system that could generate feasible 3D printable designs. Despite being one of the most technically demanding projects I have undertaken due to the numerous constraints, the design process taught me an immense amount in both technical and conceptual development.
Role
Designer, Renderer
Credits
Concept, Direction // Marjan Colletti
3D Print // University of Innsbruck
3D Print // University of Innsbruck
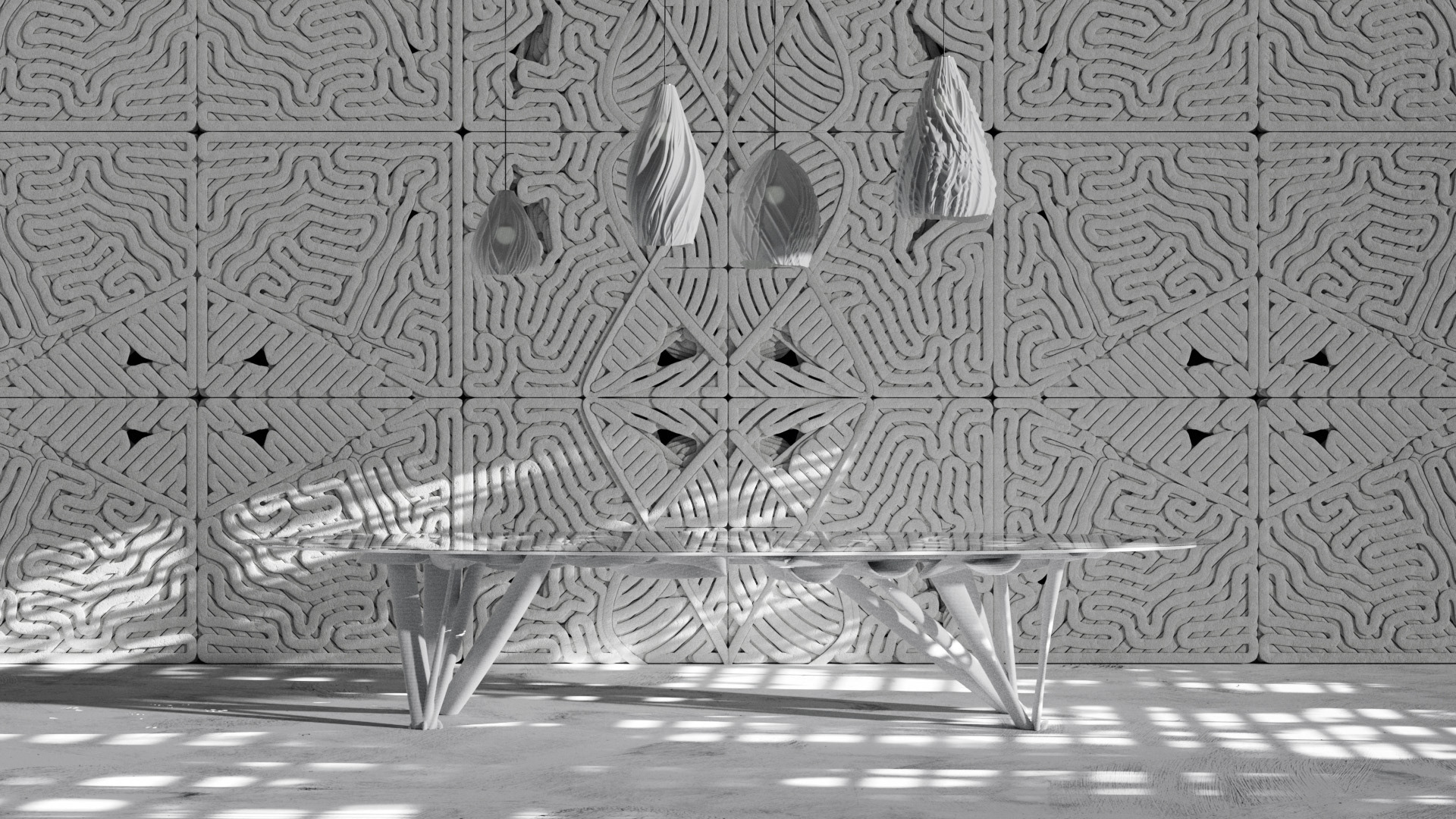
Visualisation of Colletti table, designed lamps and this project's design in the same space.
A key concept involved incorporating interweaving and diagonal layers that intersected the typical flat layers. This approach aimed to enhance the strength and dimensionality of the concrete wall panel, addressing concerns related to stability and weight, while keeping in touch with perforation. In addition, a steel wire-reinforced concrete tube was integrated to connect all the layers.
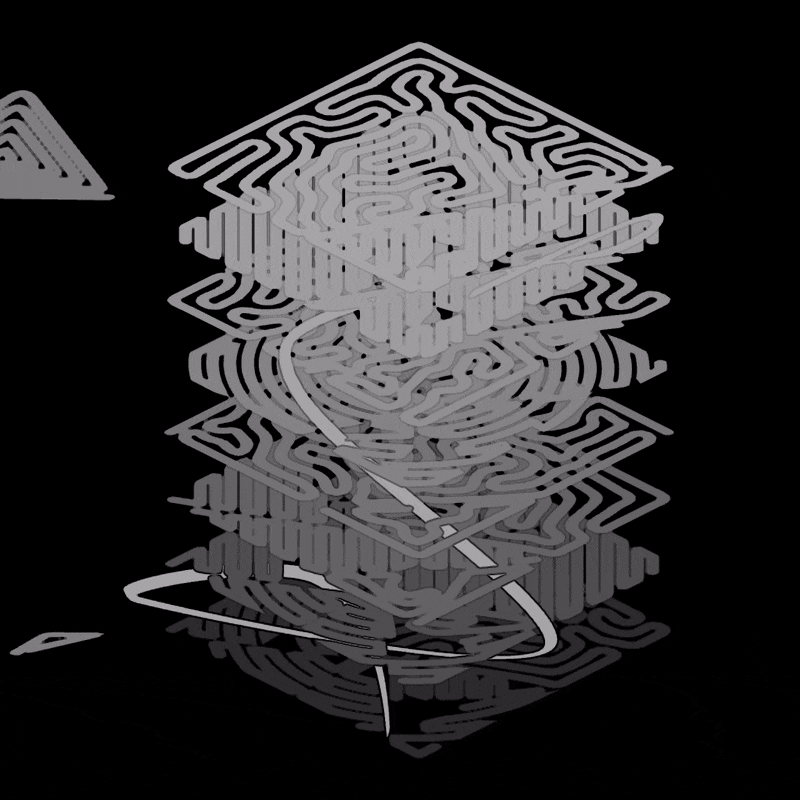
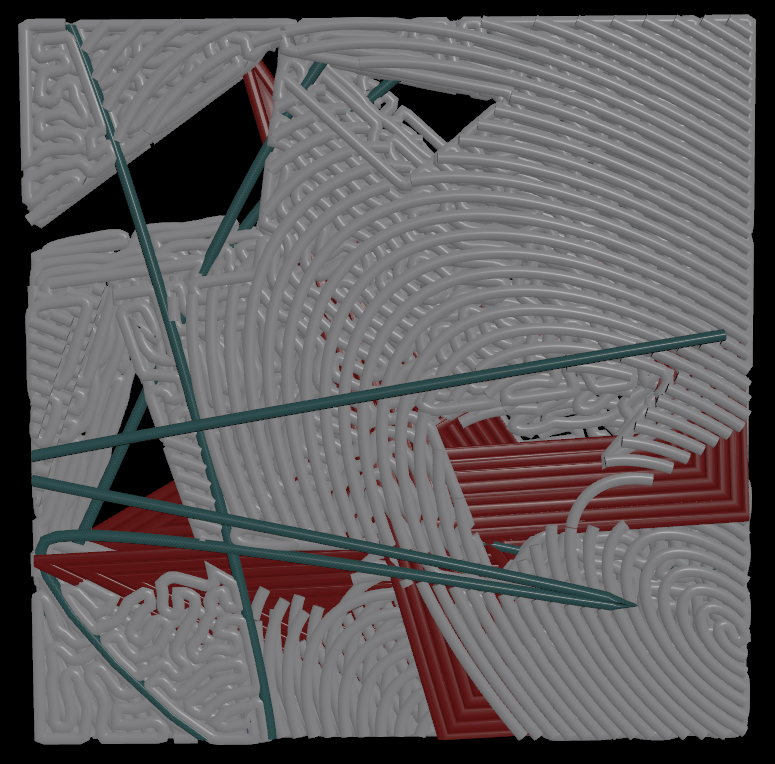
WIP 01
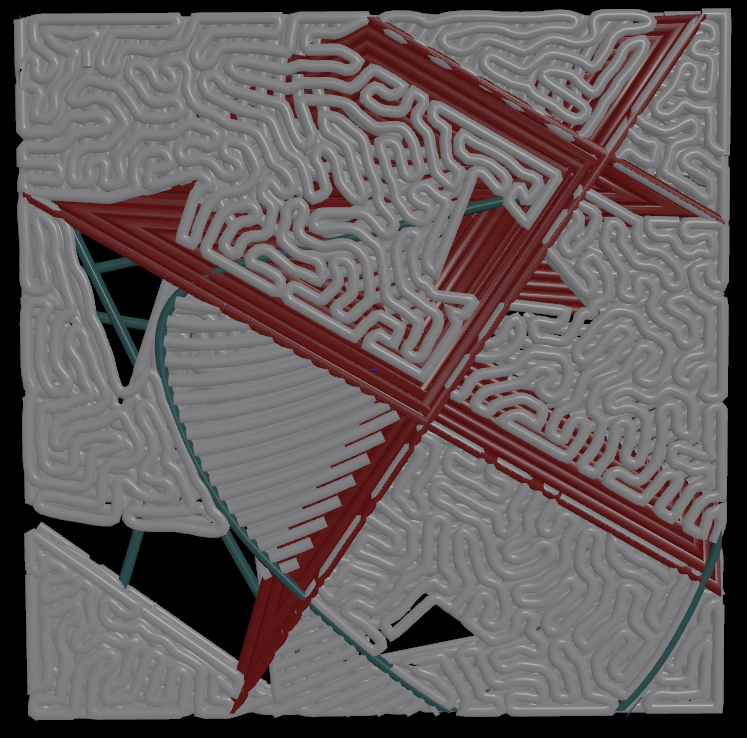
WIP 02
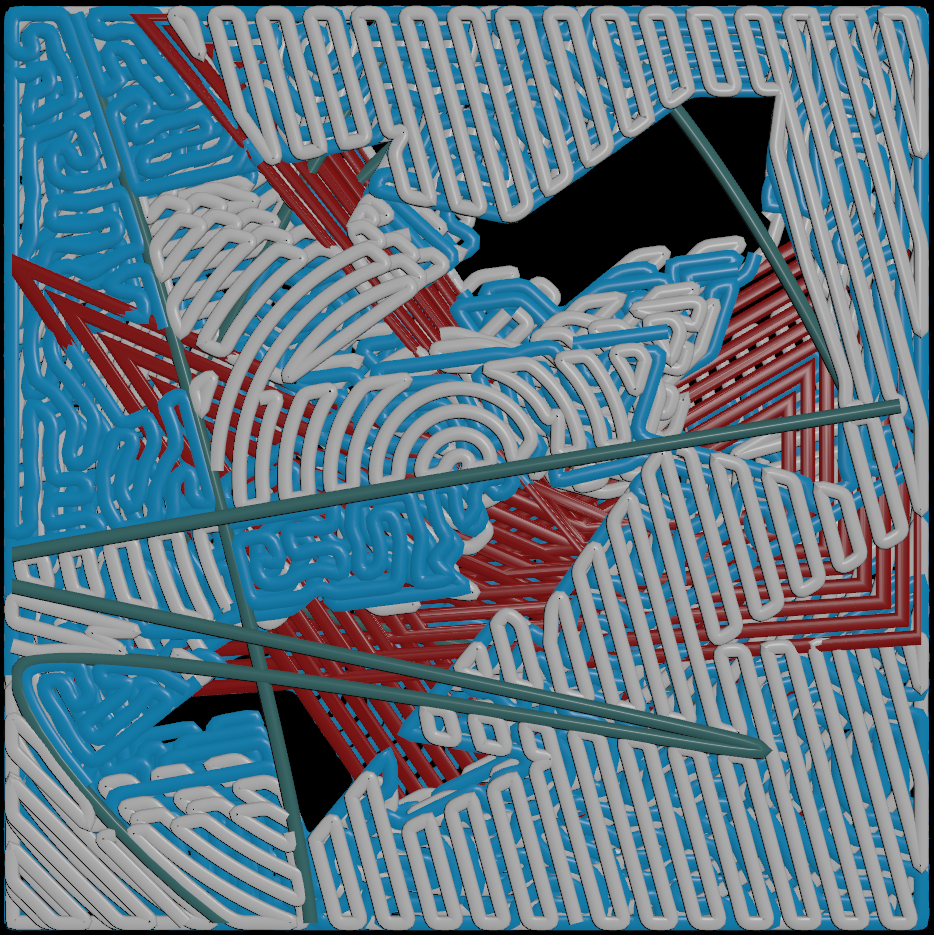
WIP 03
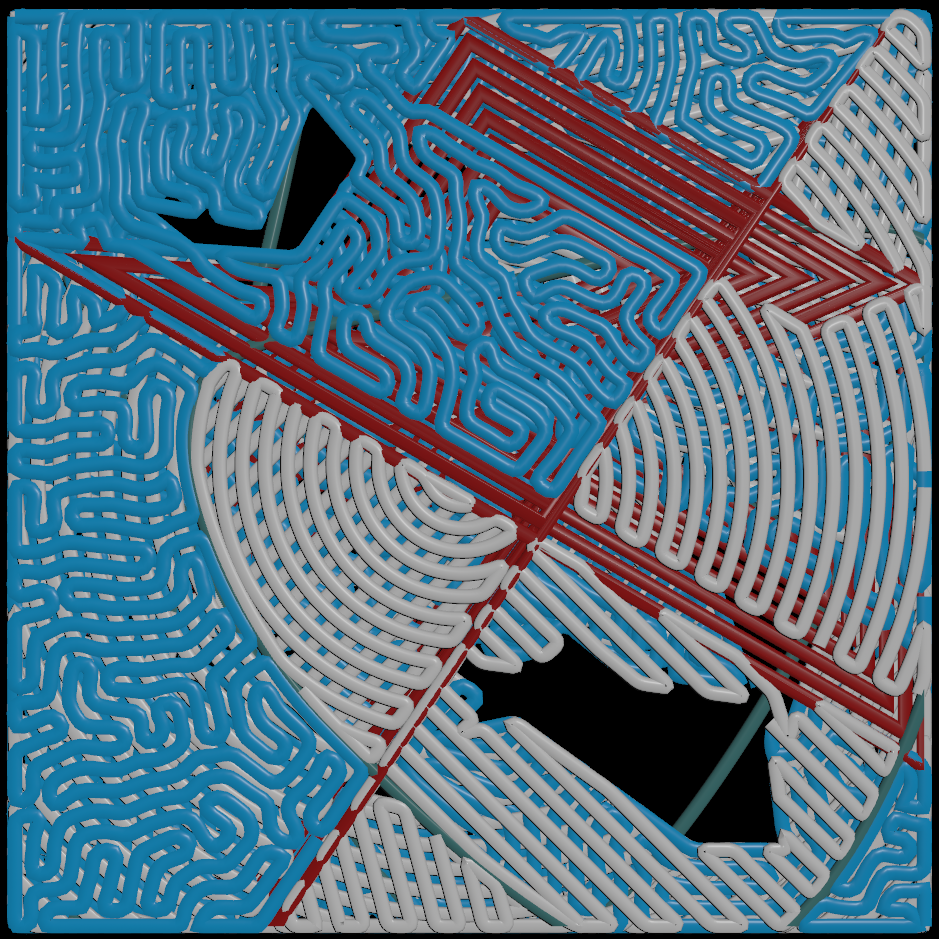
WIP 04
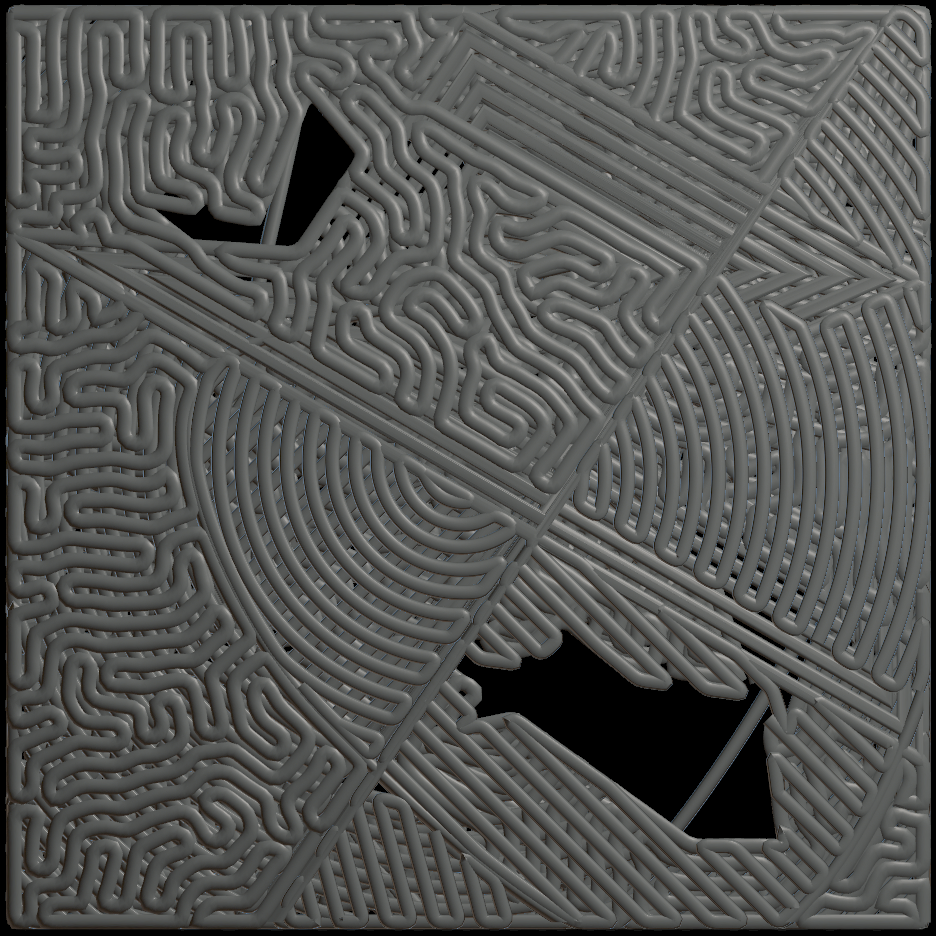
WIP 05
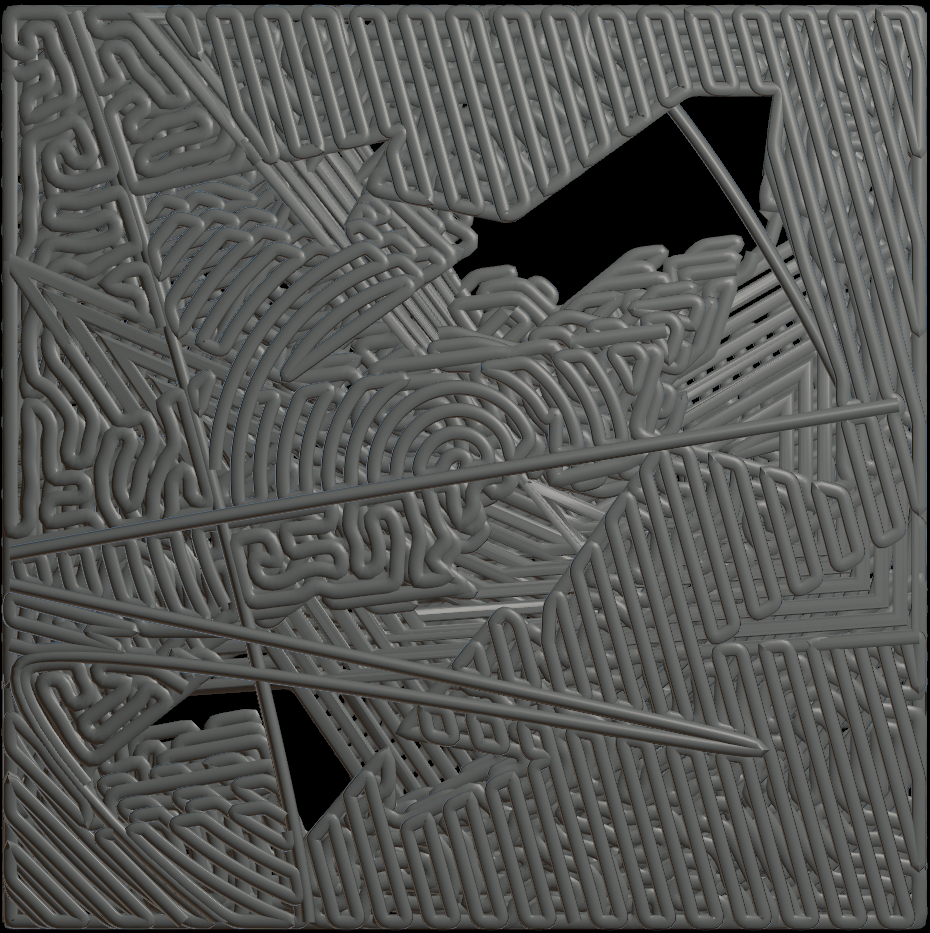
WIP 06
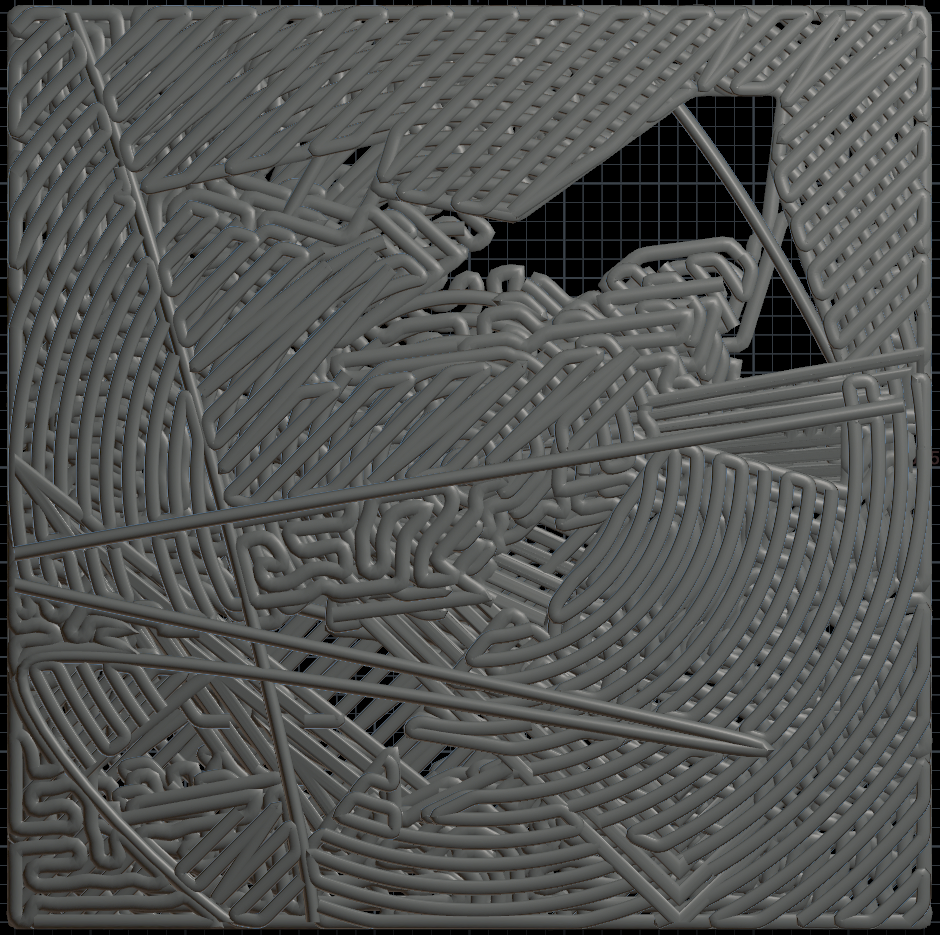
WIP 07
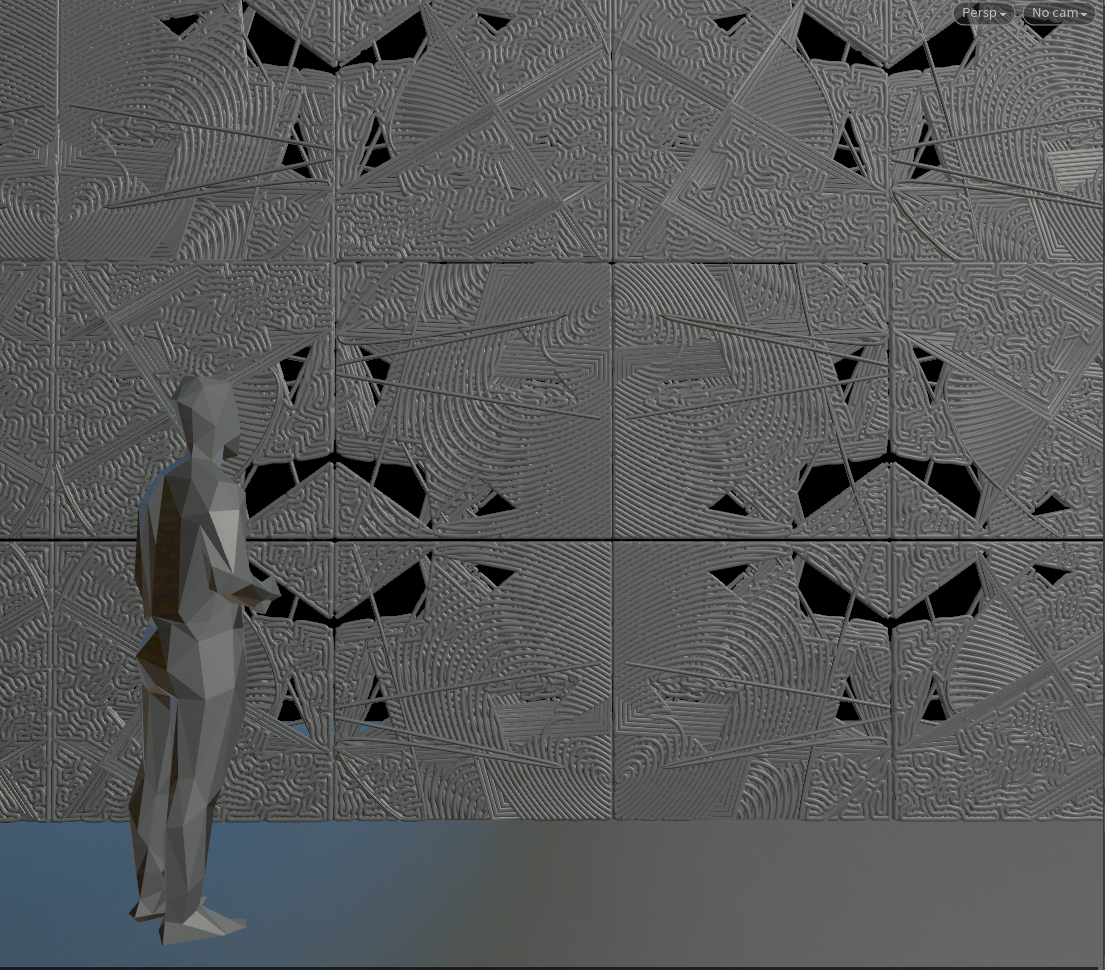
WIP 08
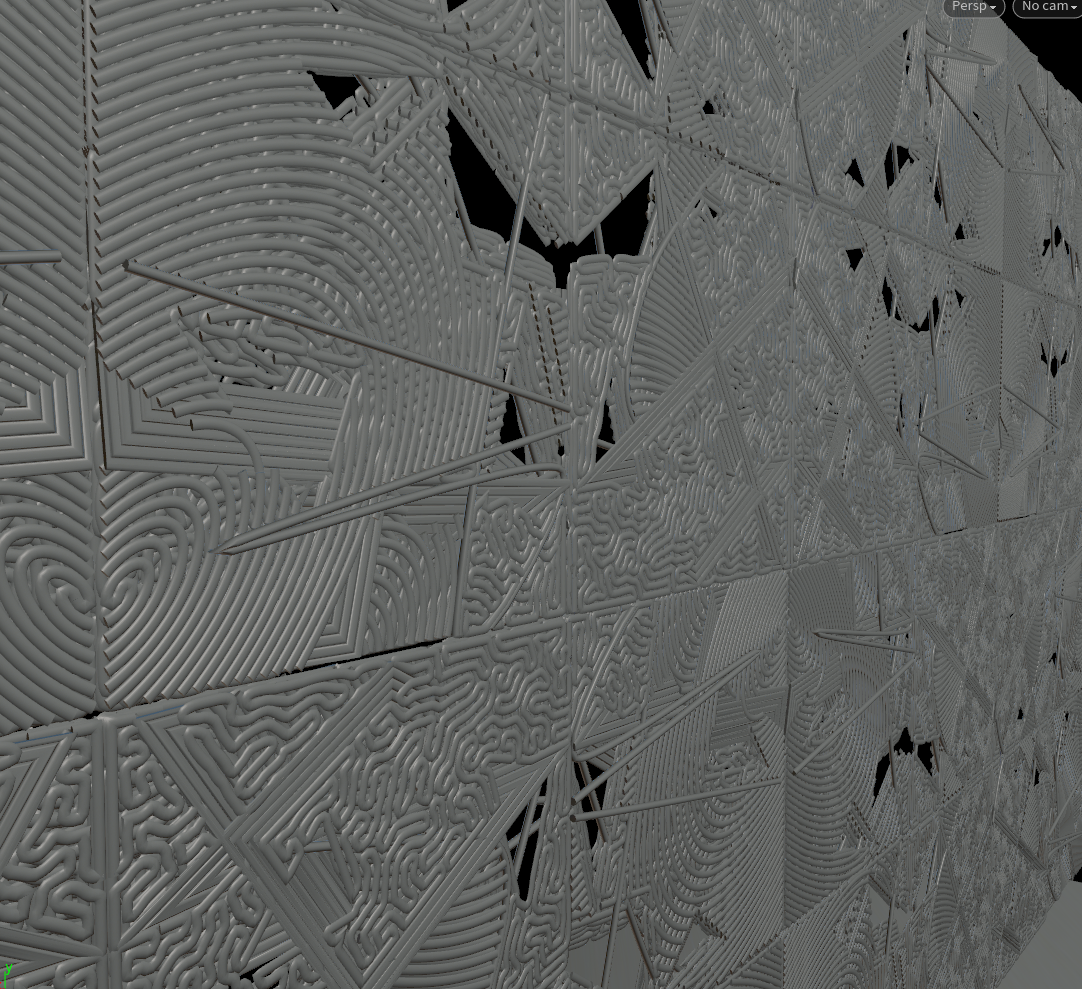
WIP 09
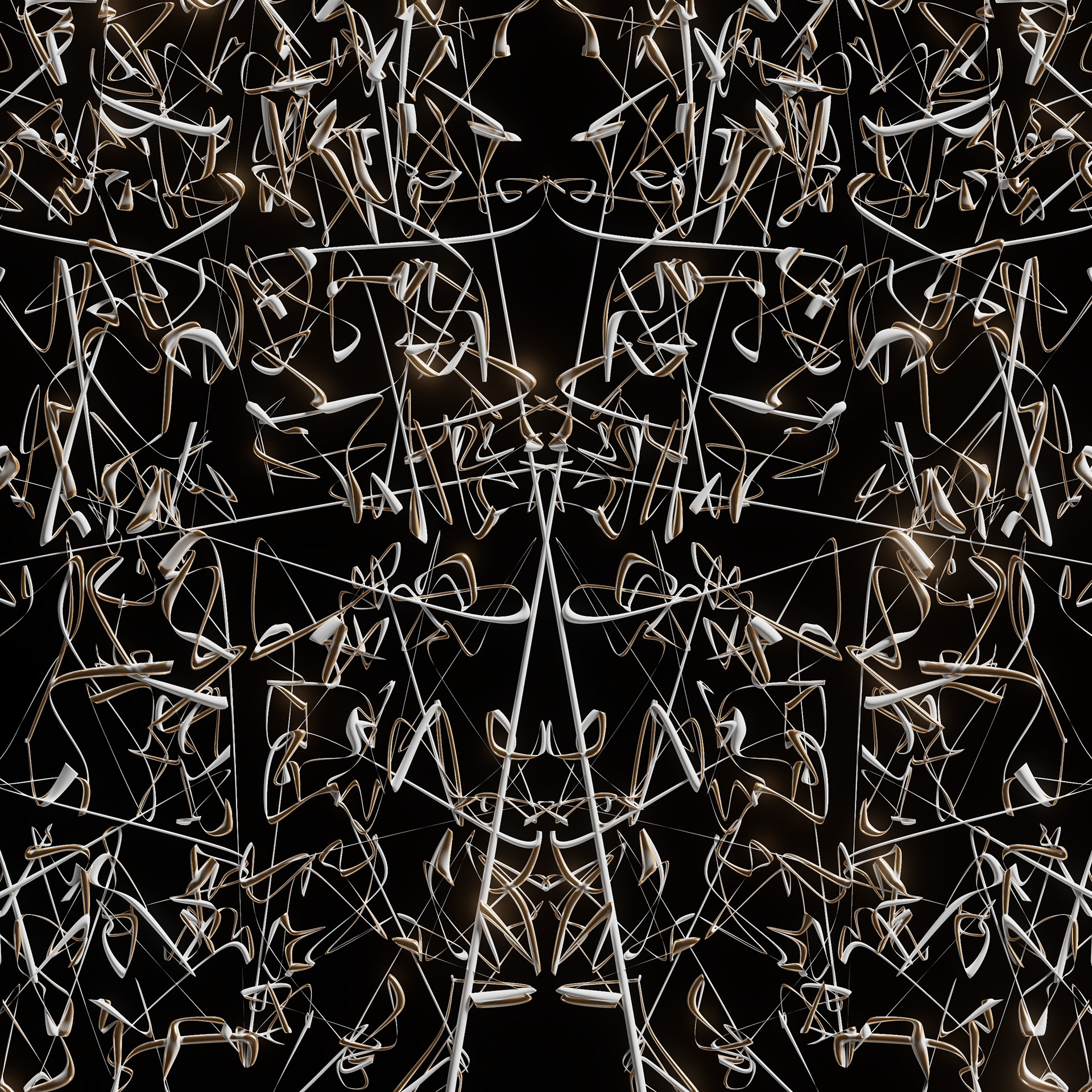
Concept 01
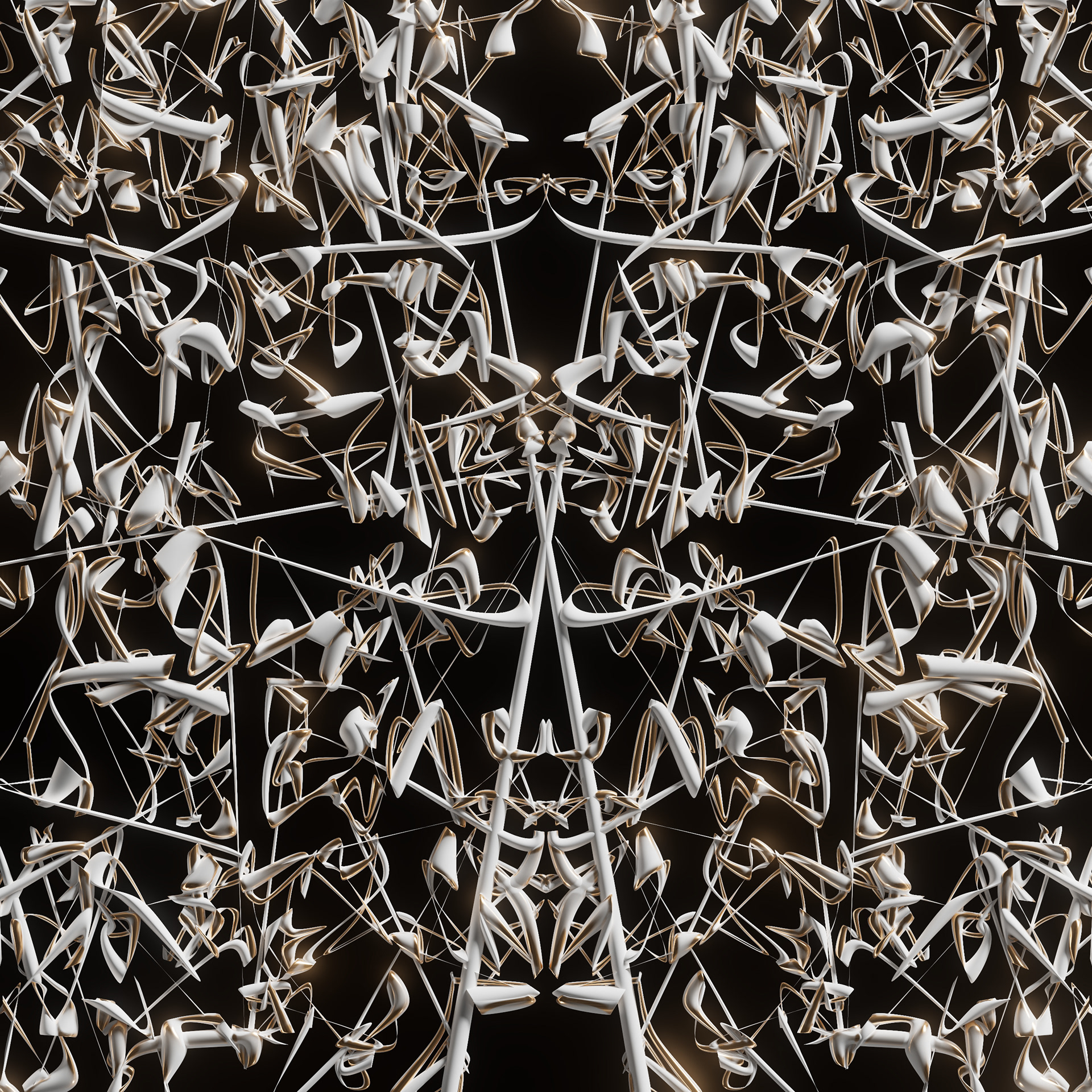
Concept 02
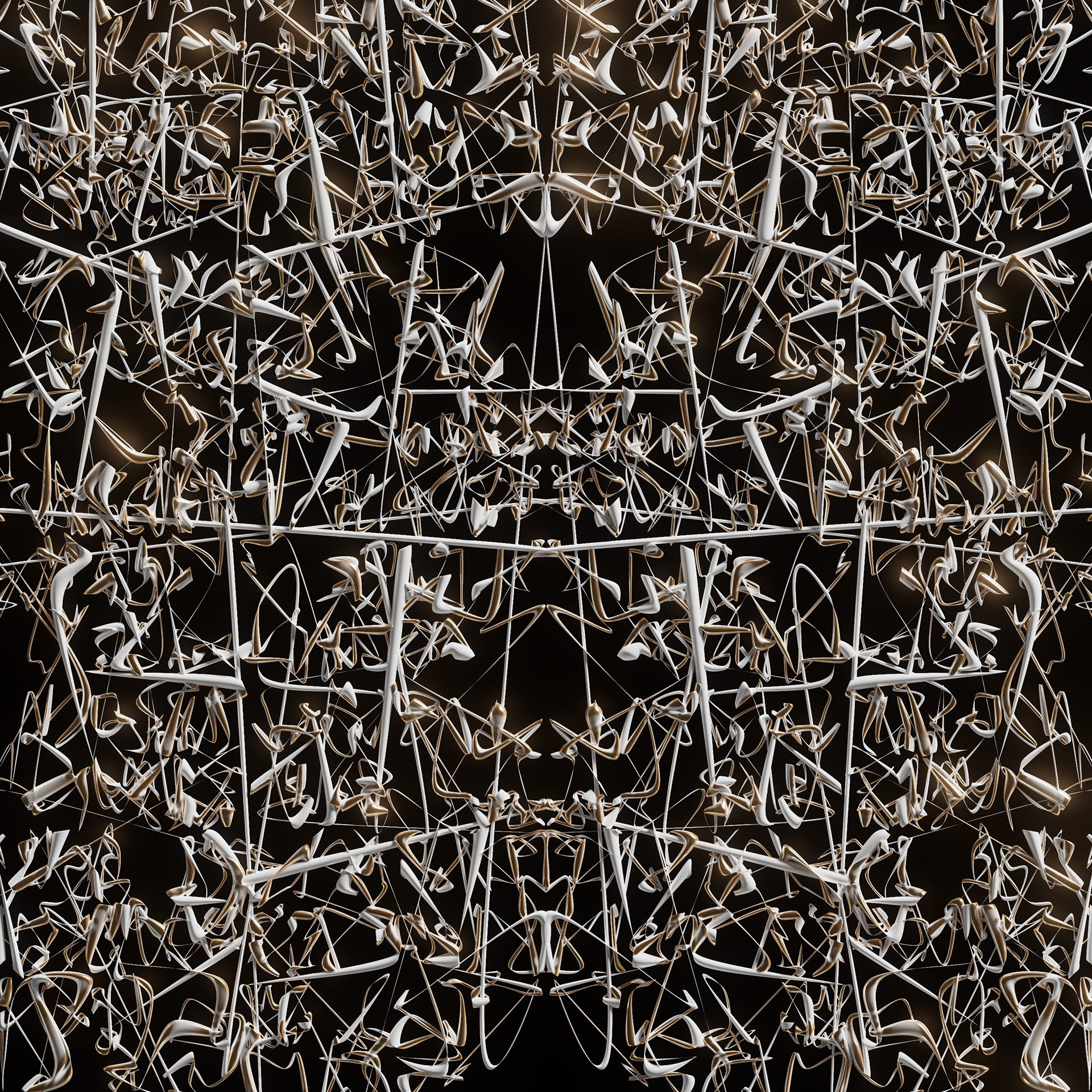
Concept 03
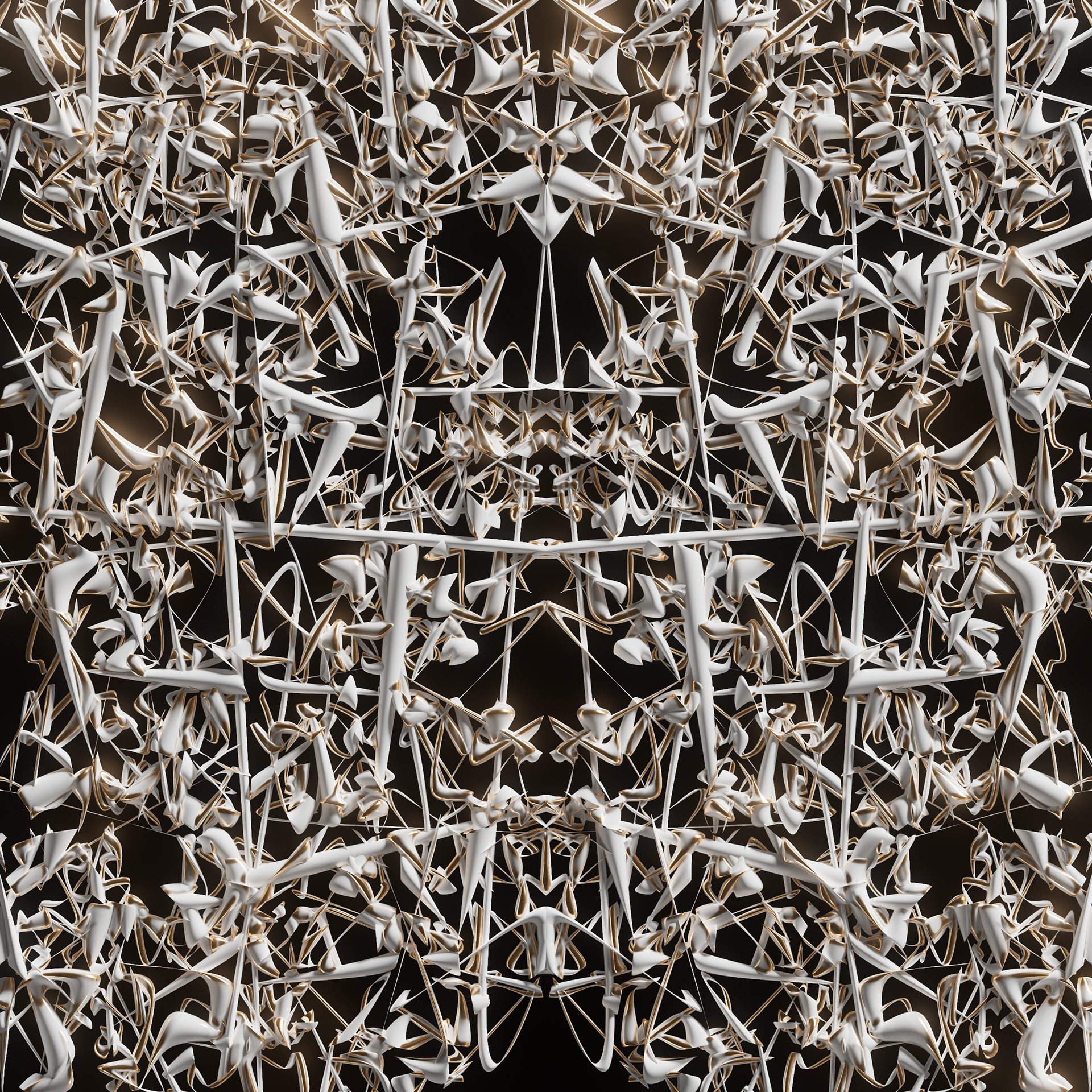
Concept 04
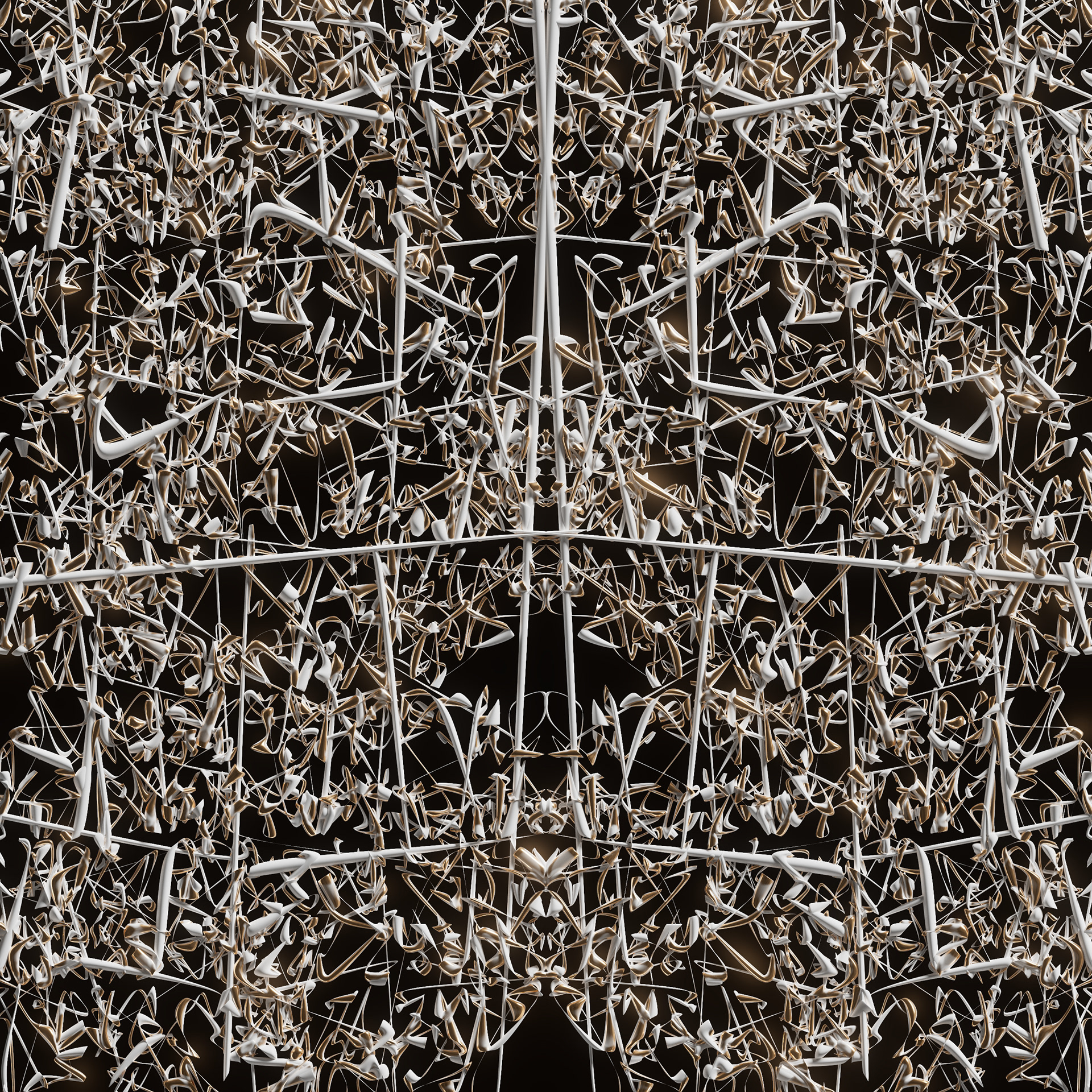
Concept 05
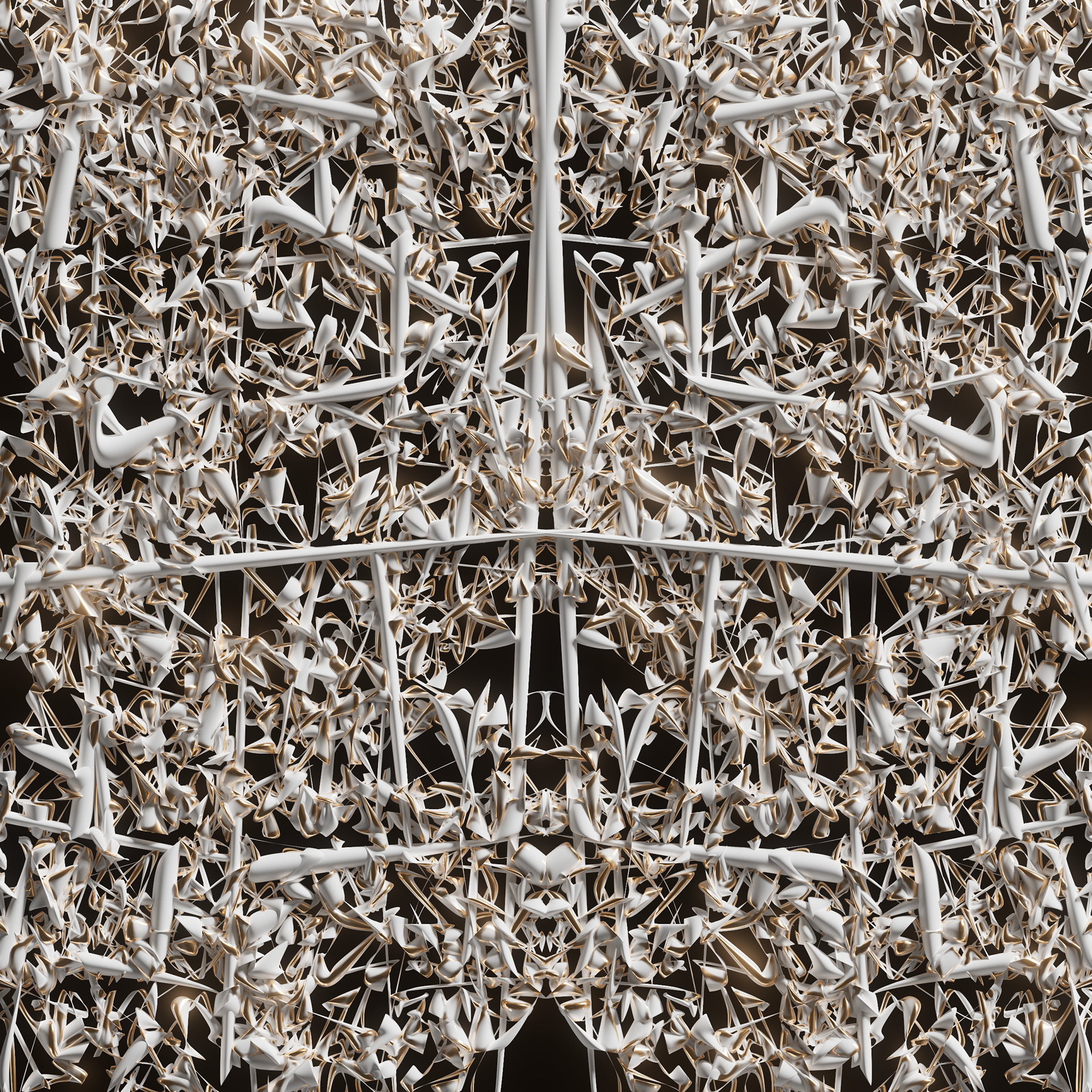
Concept 06
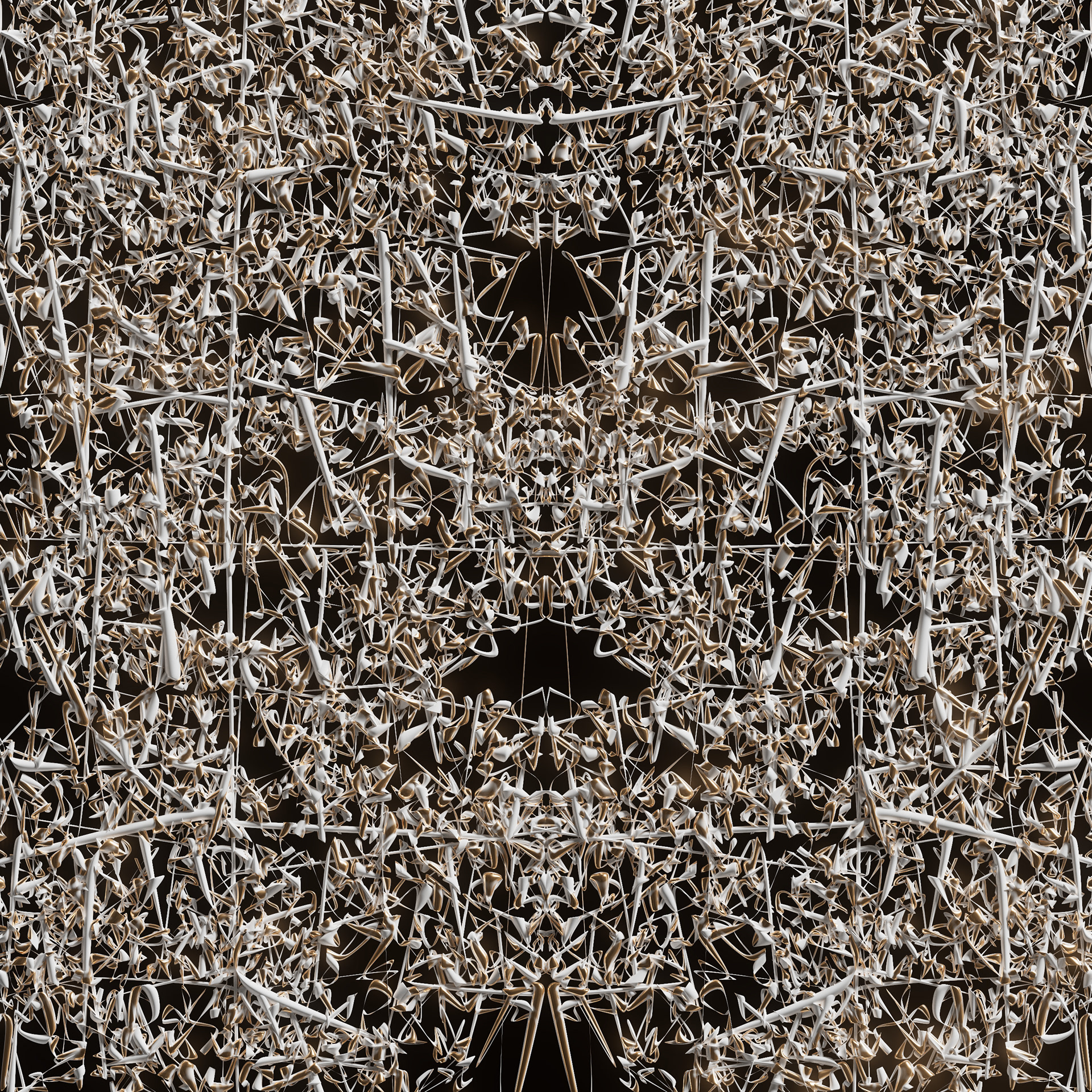
Concept 07
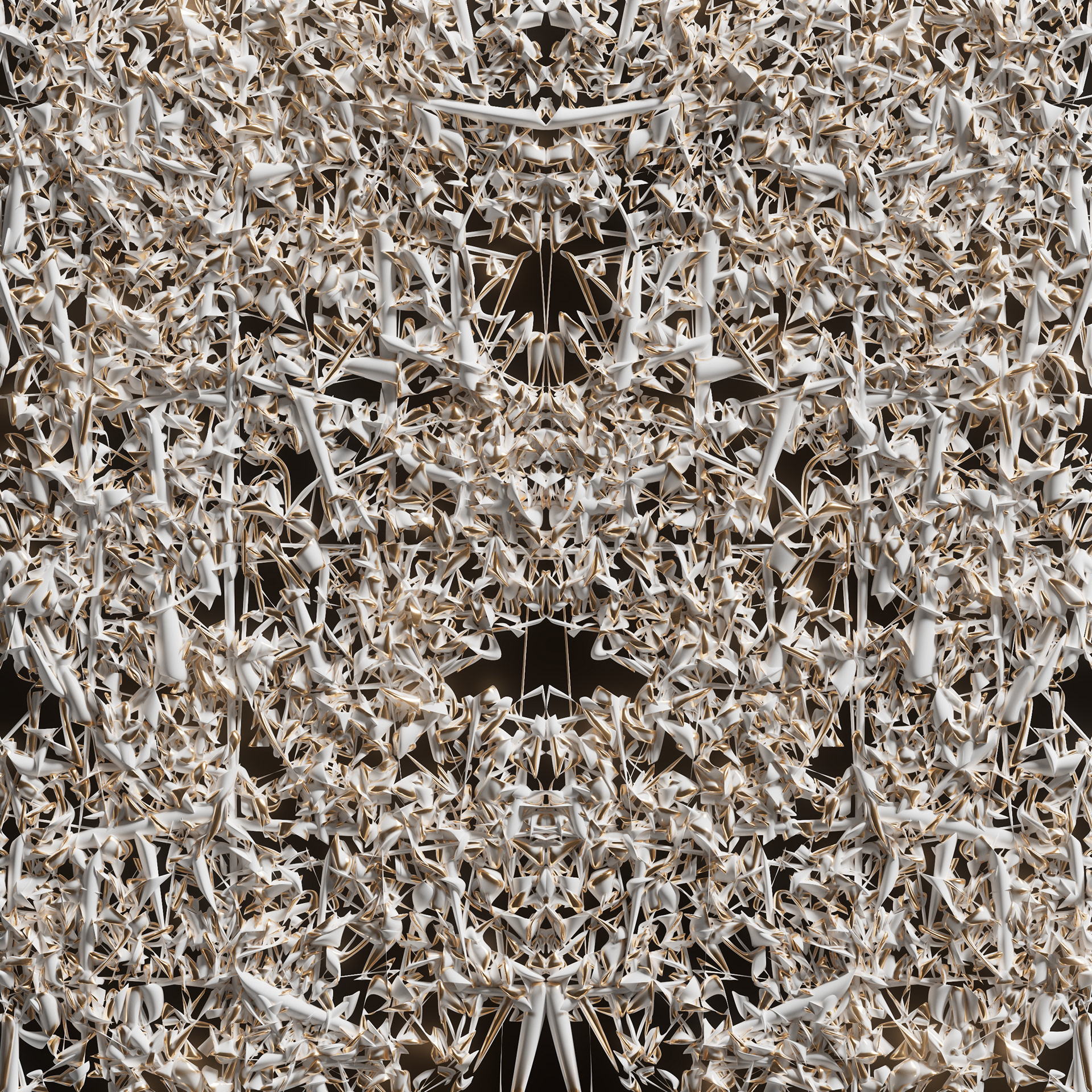
Concept 08
While initial concepts involved using techniques directly from the RnD of PDNB, further refinement was required to adapt to the constraints of the project, namely tool path feasibility. Each time the nozzle deposits wet concrete onto the print bed, a tool path that is continuous, a start and an end point are required to minimise extra deposition of material. To create a more consistent surface, start/end points had to be minimised. This led to the design utilising differential growth systems, which were compatible with the constraints. Additional languages were introduced to inject visual diversity, this included fingerprint-like spirals and hatching.
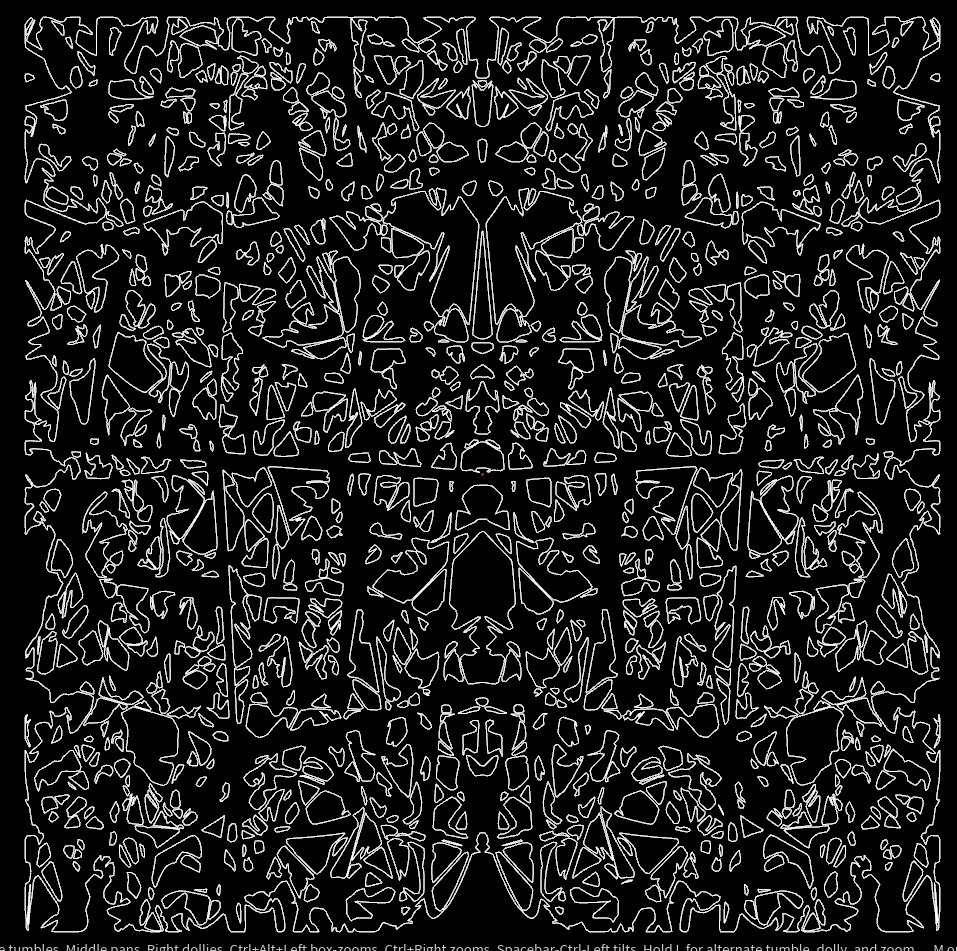
Toolpath Viz 01
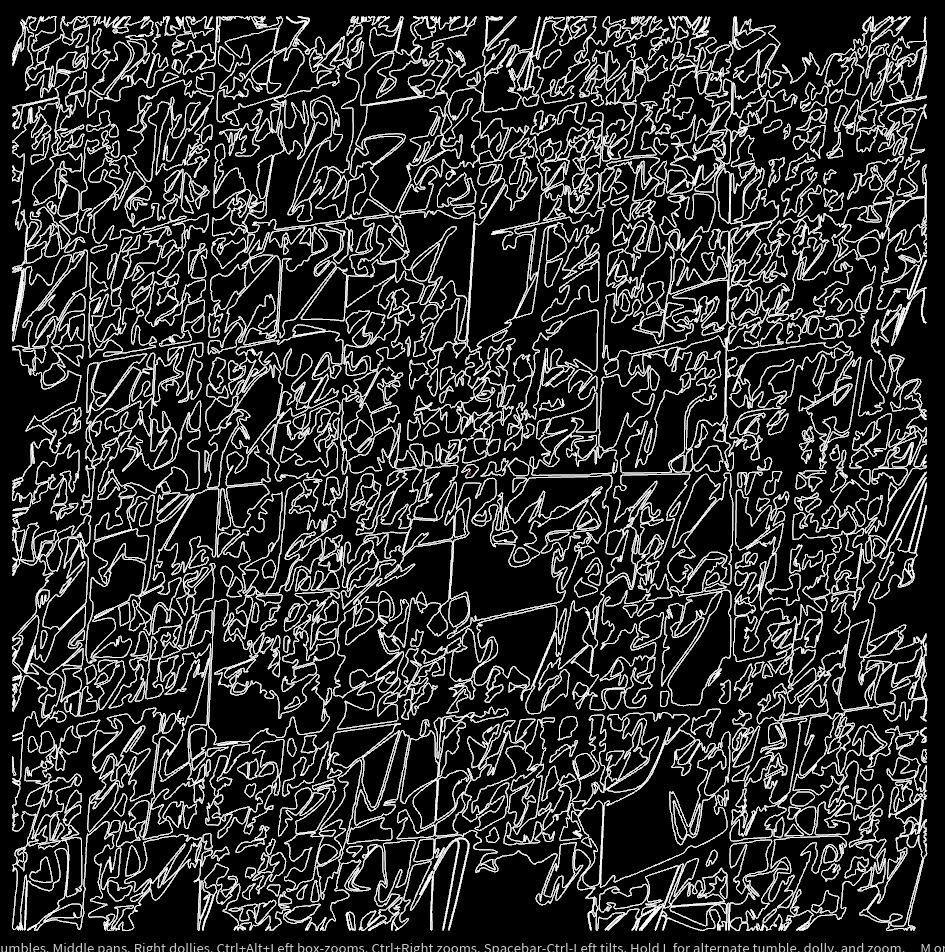
Toolpath Viz 02
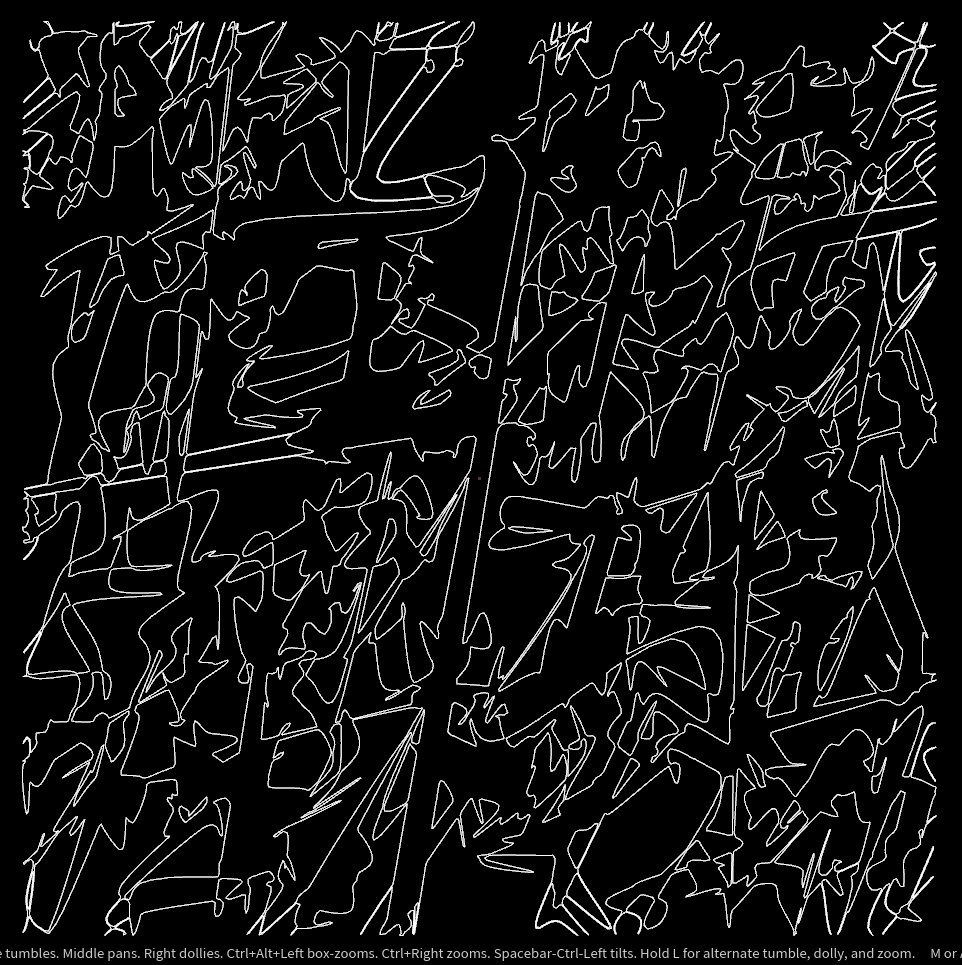
Toolpath Viz 03
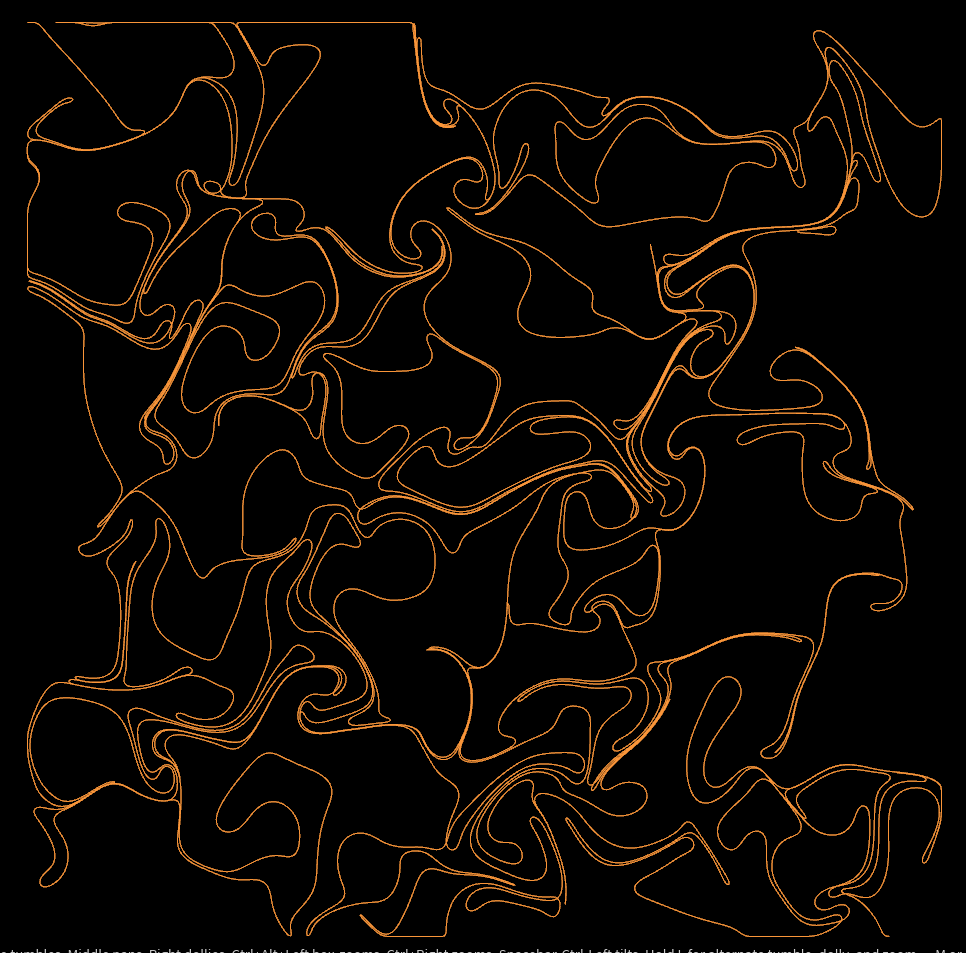
Toolpath Viz 04
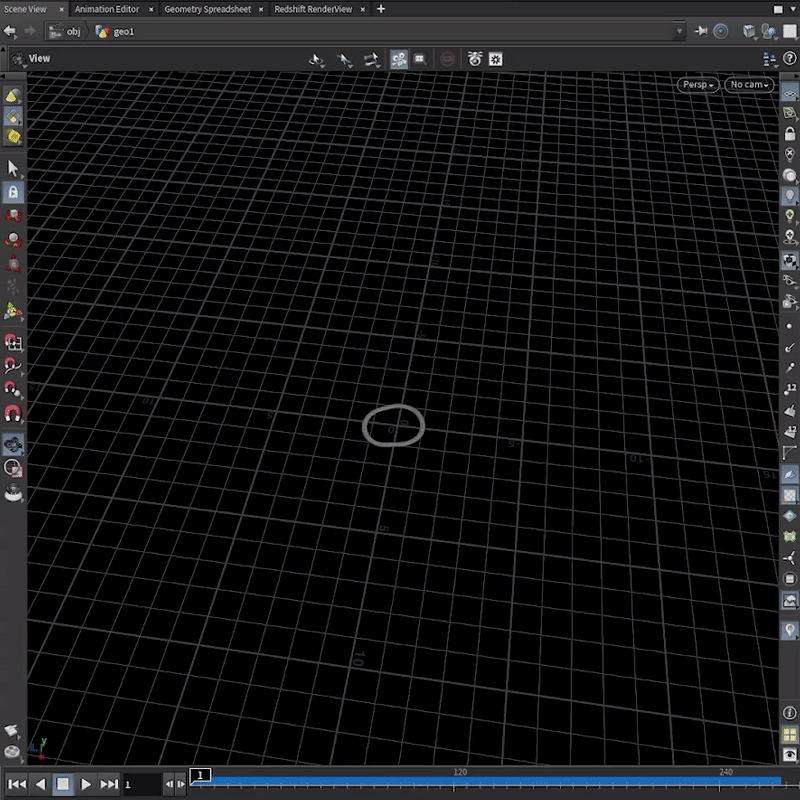
Differential growth 01
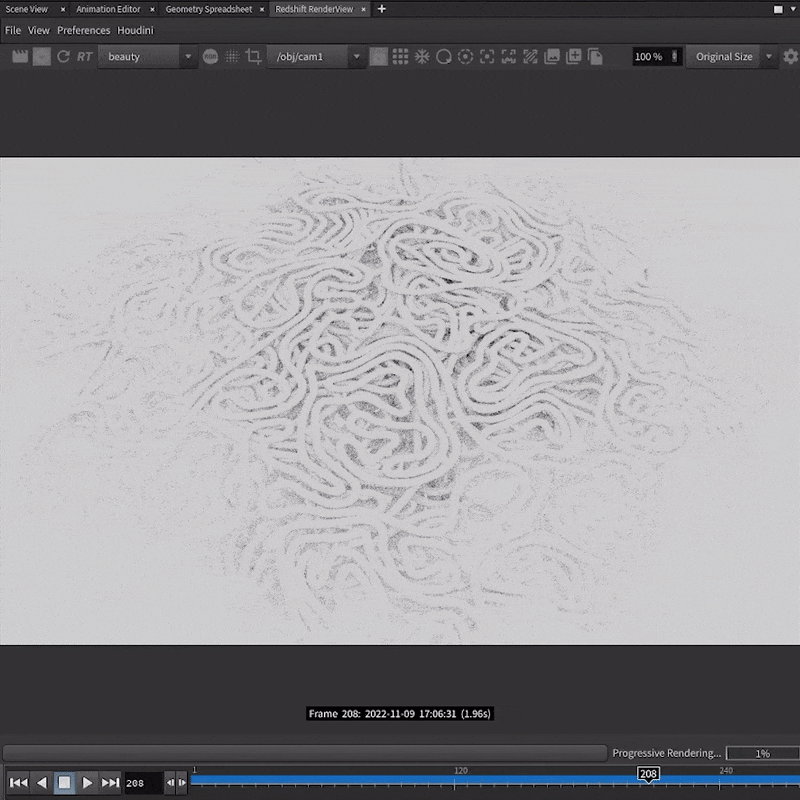
Differential growth 02
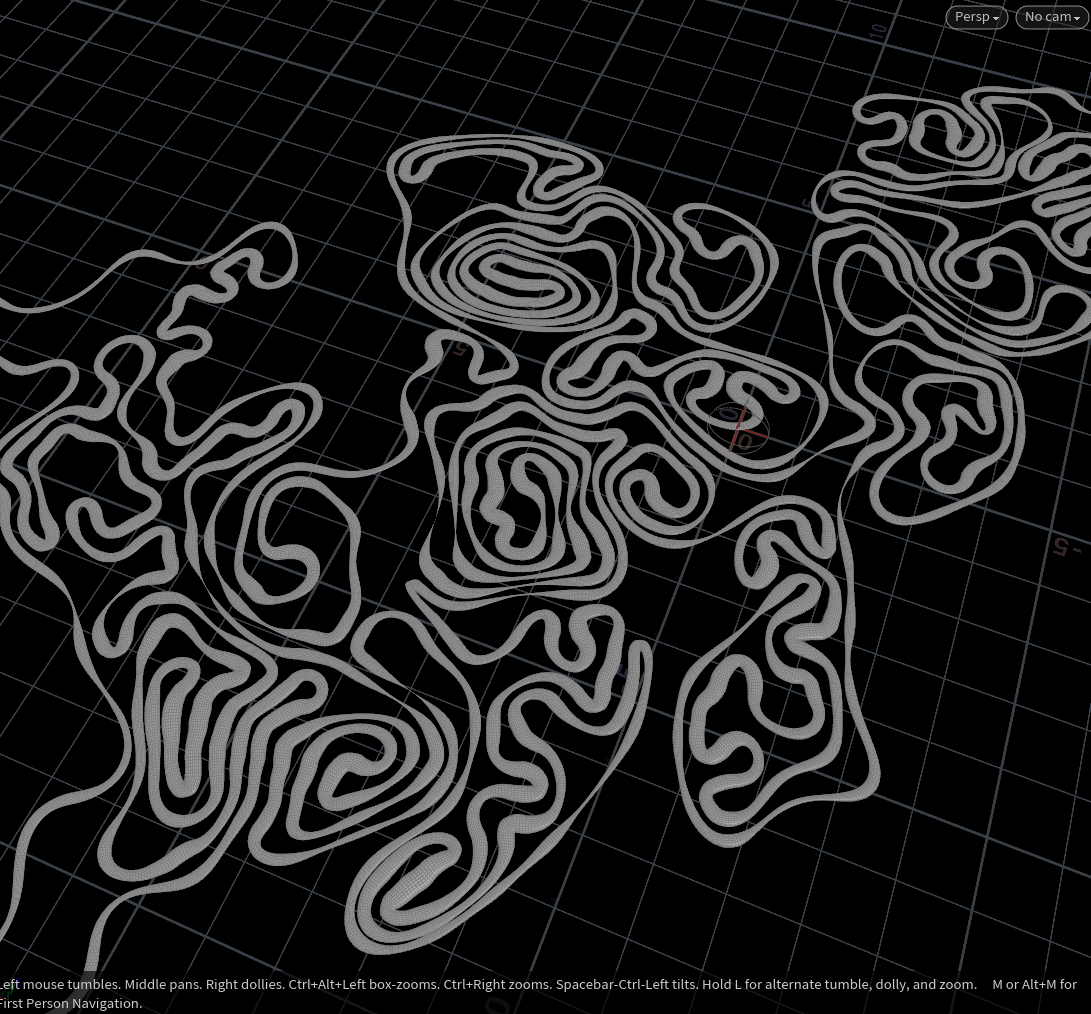
Differential growth 03
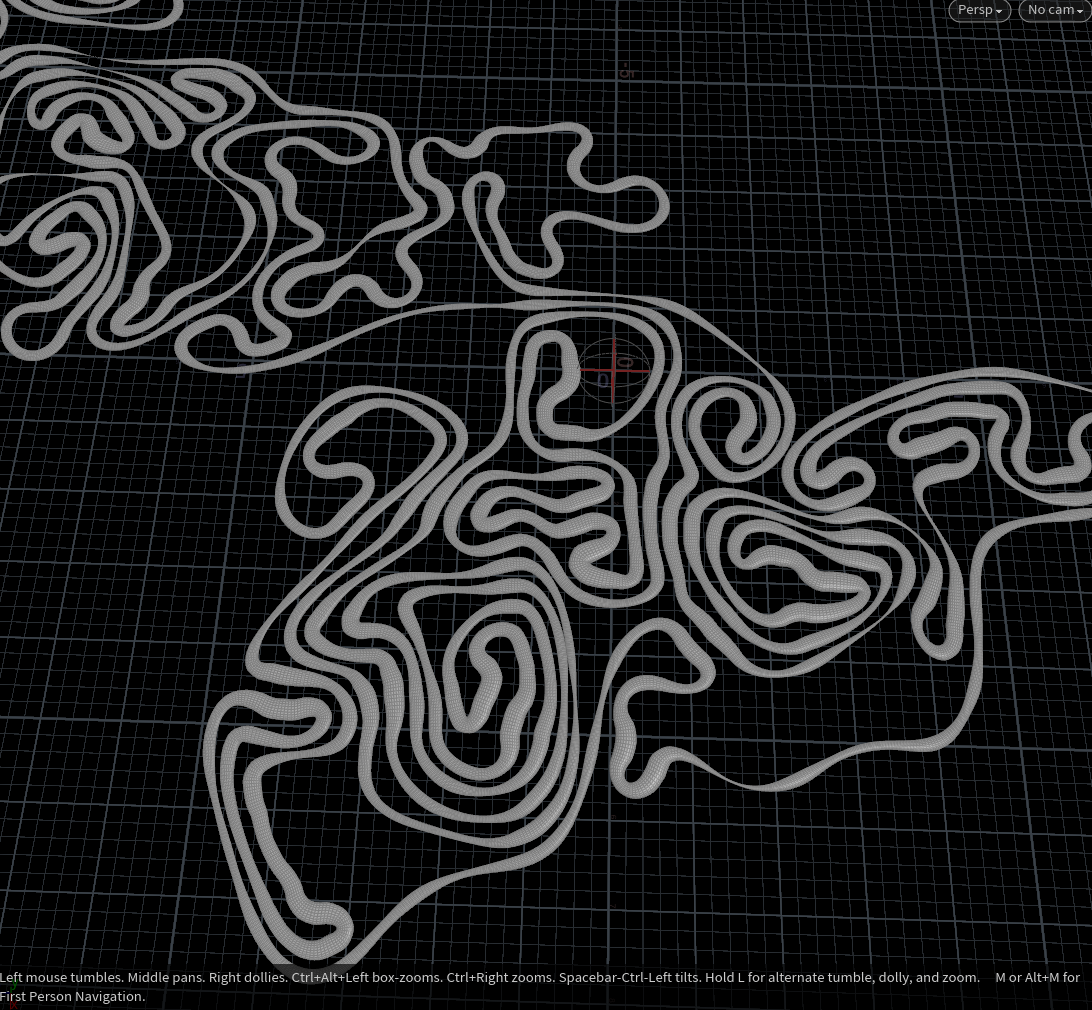
Differential growth 04
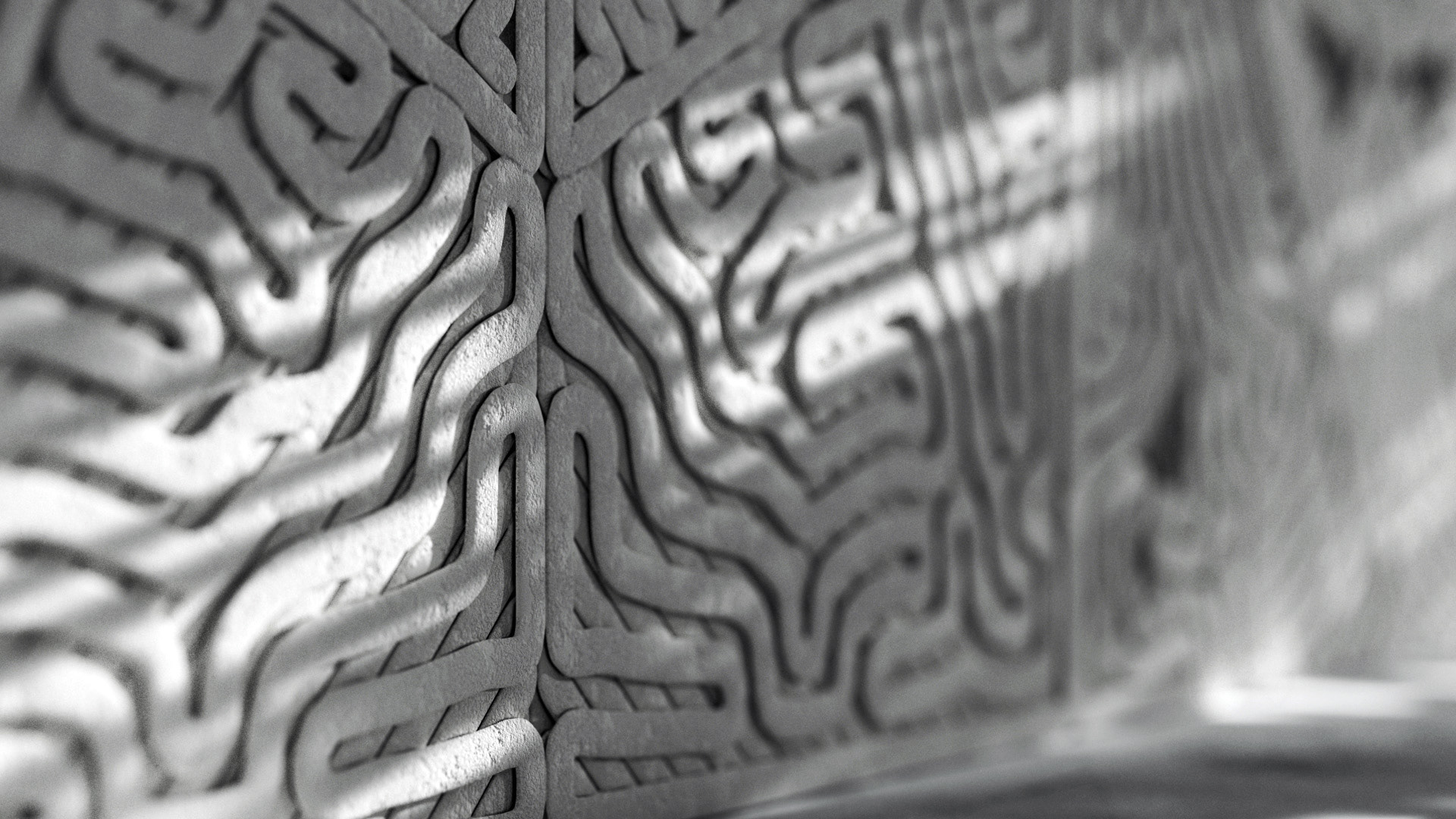