Synopsis
The project involved creating a small collection of lampshades that would be printed with a 6-axis 3D printer. The concept stemmed from the RnD work of PDNB, which evolved into a more minimal design of the spiralling folds through a series of iterations. To introduce three-dimensionality and complexity, layers of folds at different depths and directions were incorporated.
While this project produced thousands of iterations with a procedural workflow, only a few handpicked designs were selected to be handed off to the 3D printing team to create a small collection. Therefore, the visuals below do not represent the final output of the month-long project.
Role
Designer, Renderer
Credits
Concept, Direction // Marjan Colletti
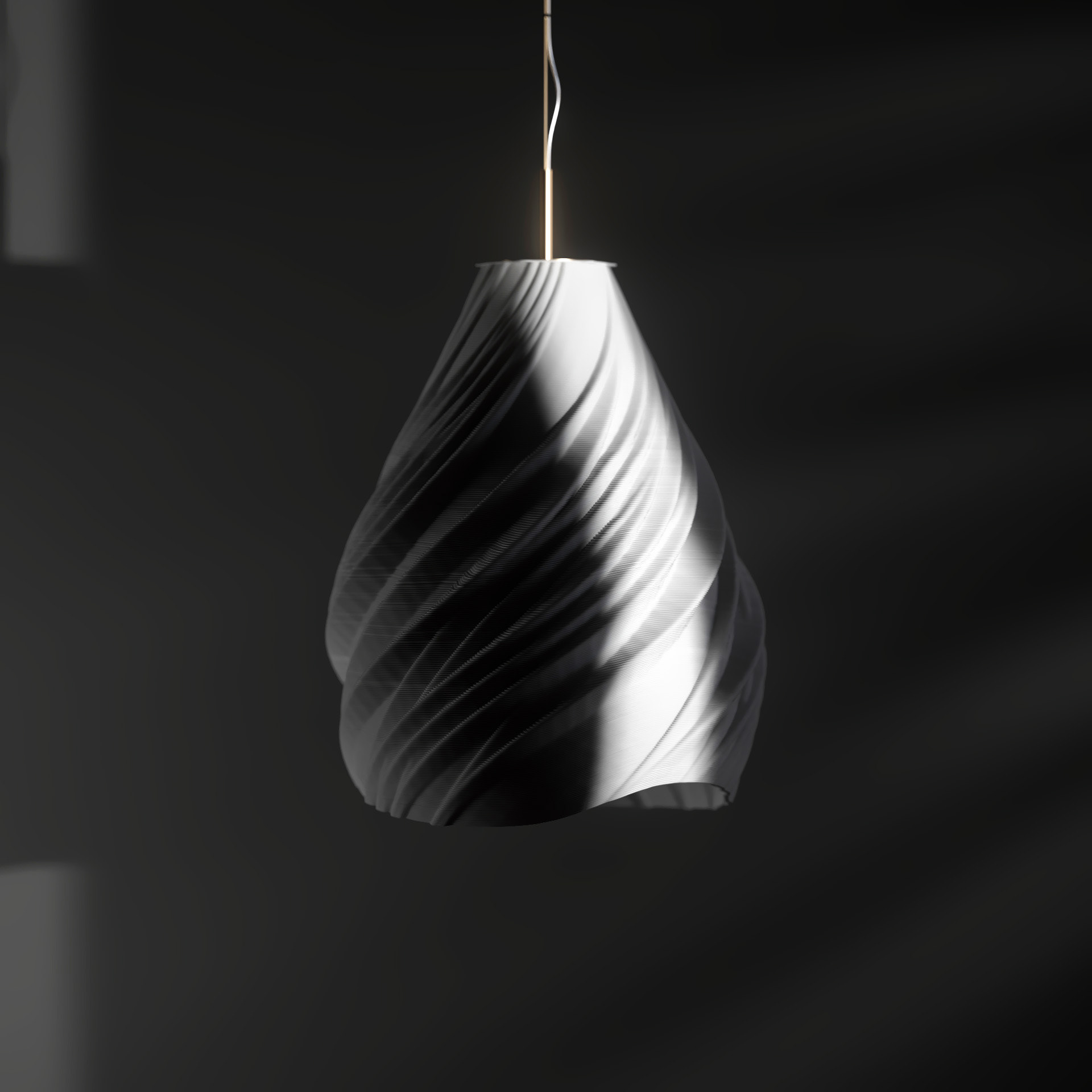
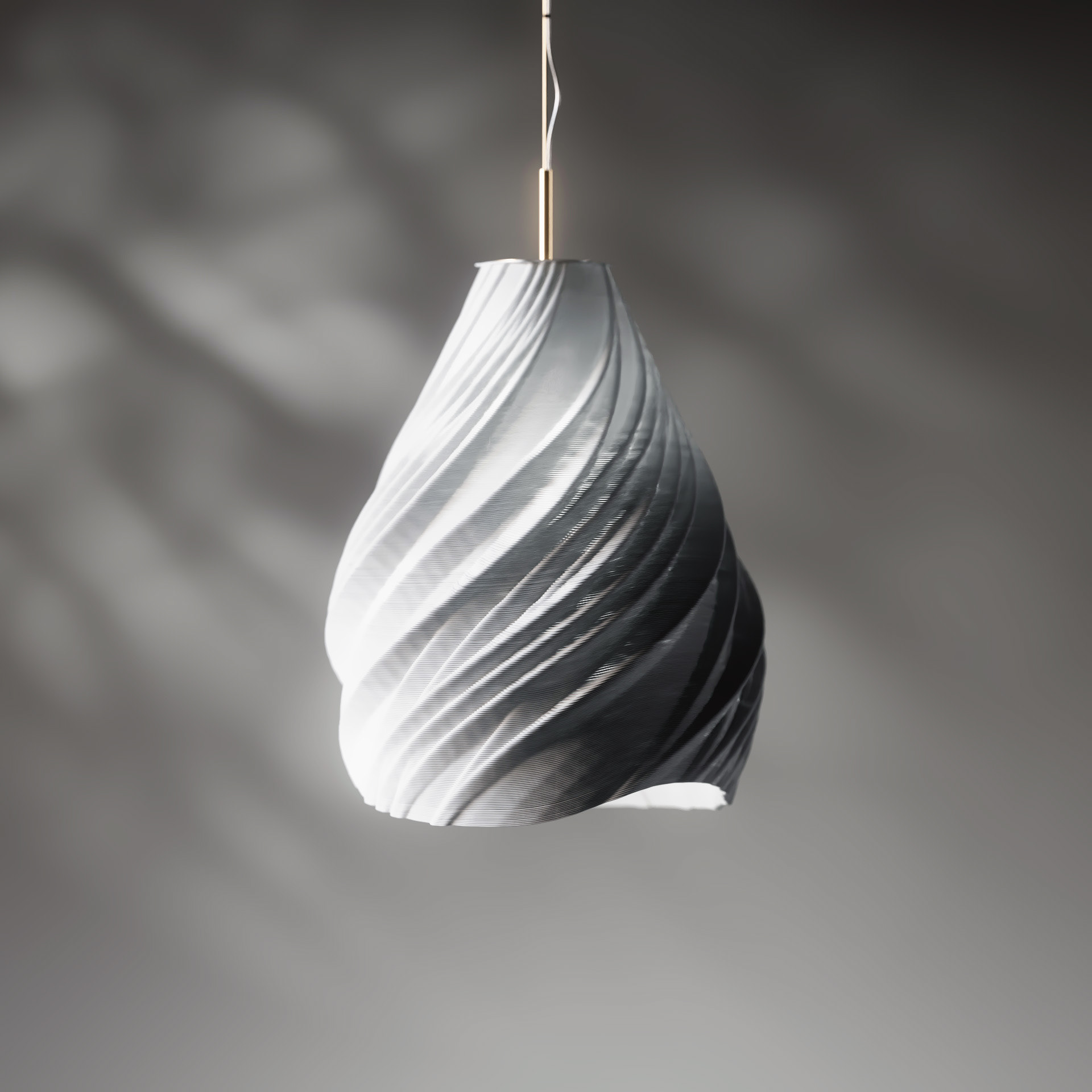
The surface of the lamp is composed of multiple layers of intricate folds. These folds interweave in a subtle manner, spiralling down the length of the lamp and creating a three-dimensionality. This visually enhances what might appear to be a simple surface, adding depth and complexity to its overall design.
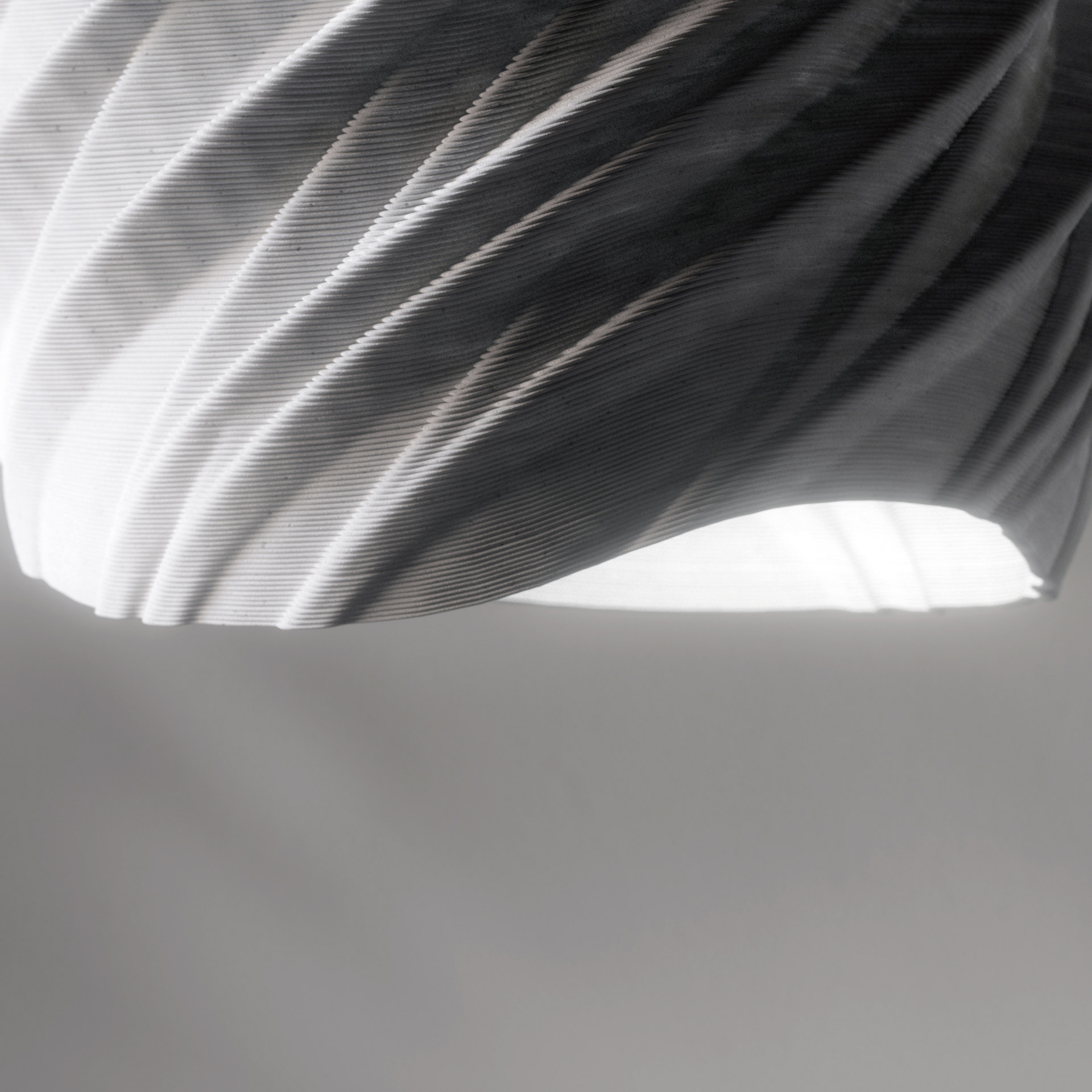
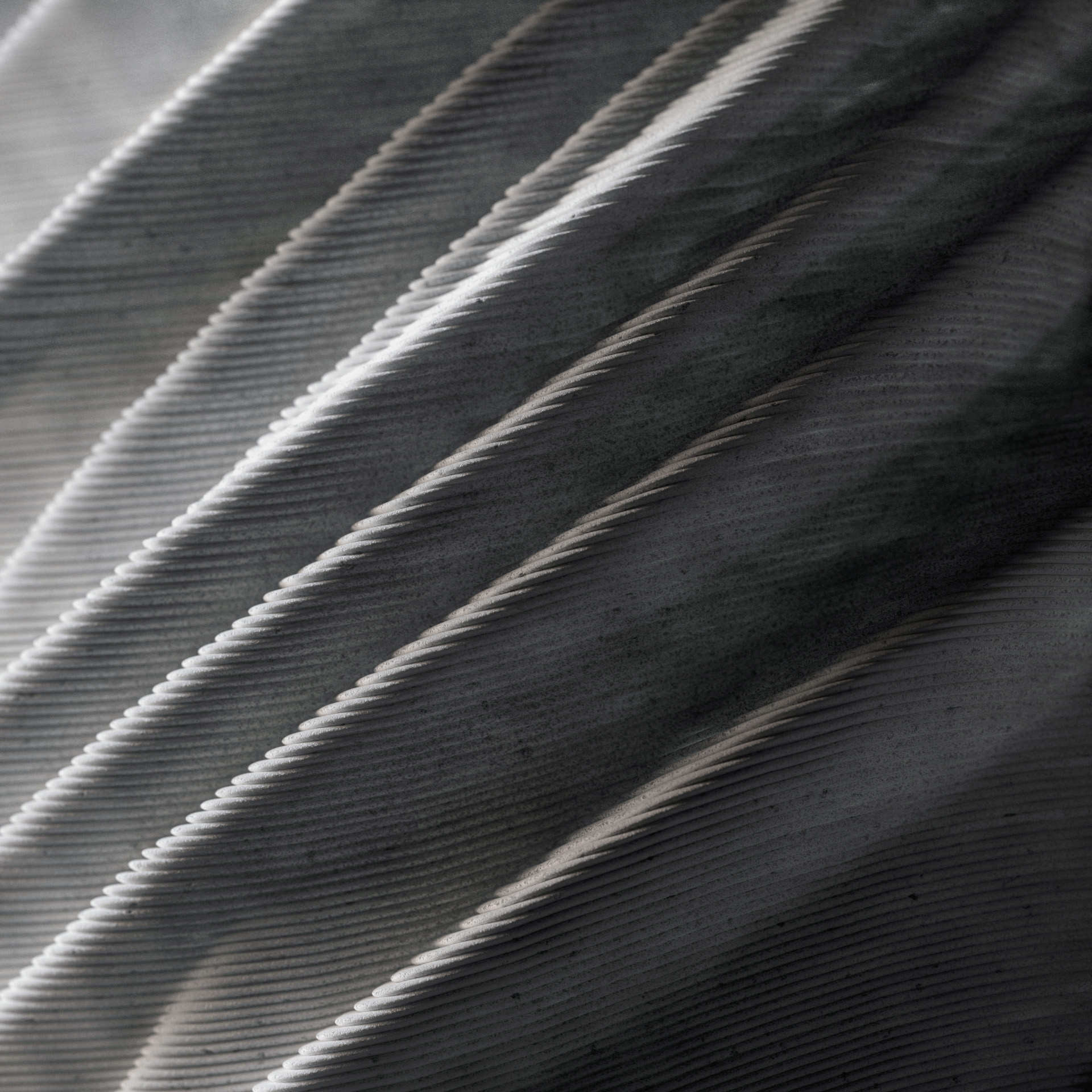
The lamp's design was specifically tailored for a 6-axis 3D printer. Although this posed certain design constraints and challenges, it also provided an opportunity to incorporate a greater degree of complexity and finesse. A few different materials were considered, including clay, recycled PET, and white and clear PLA.
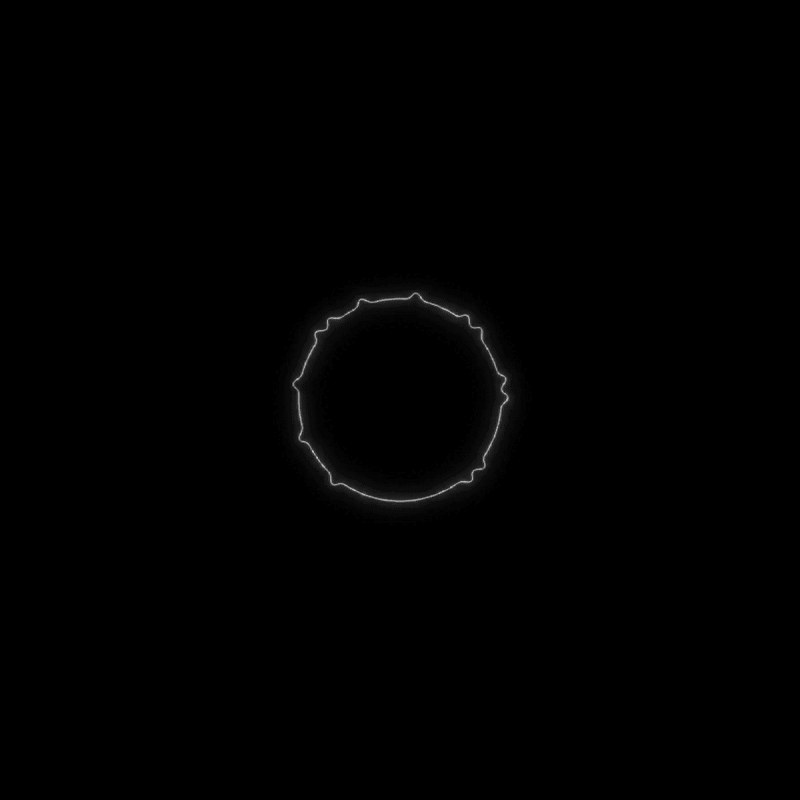
Top view // 3D print layers
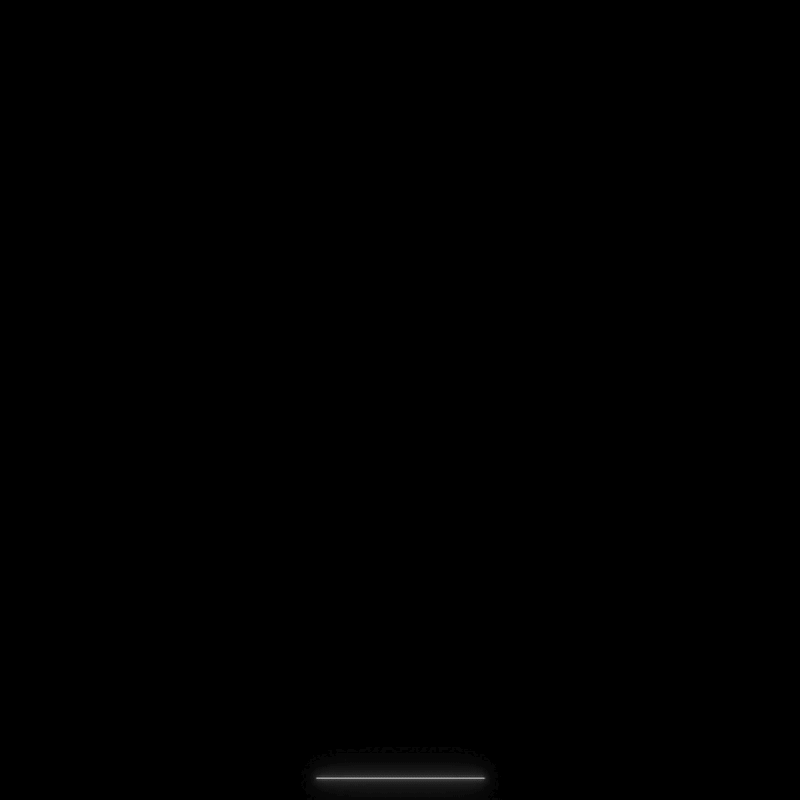
Front view // 3D print layers
This particular work was just one of hundreds of iterations in the design process and did not represent the final output of the project. The design was generated procedurally, allowing for rapid exploration of many different variations. Below are some examples that arose from this process.
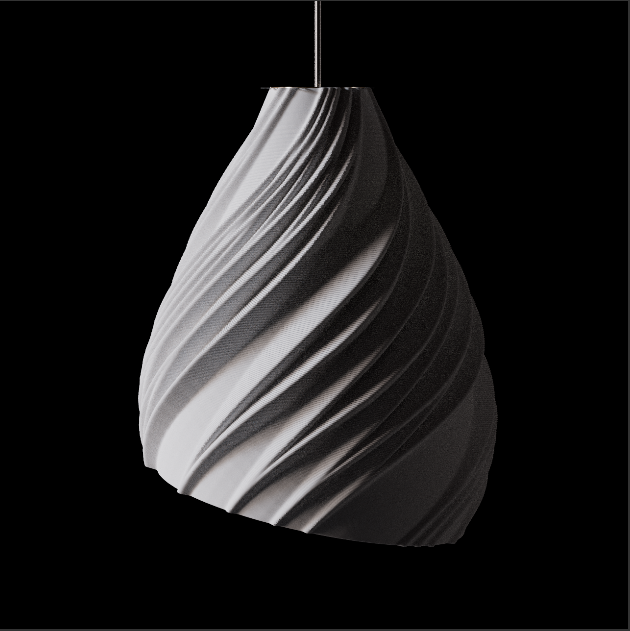
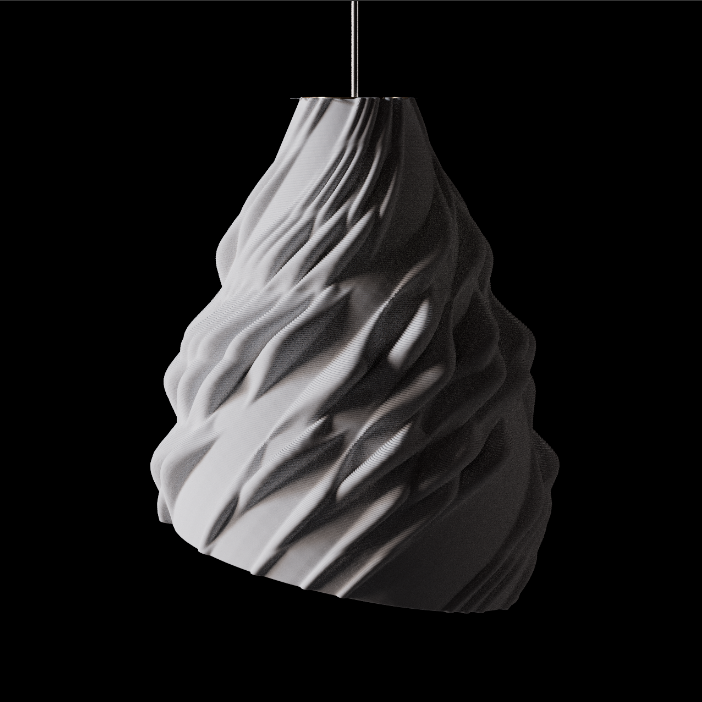
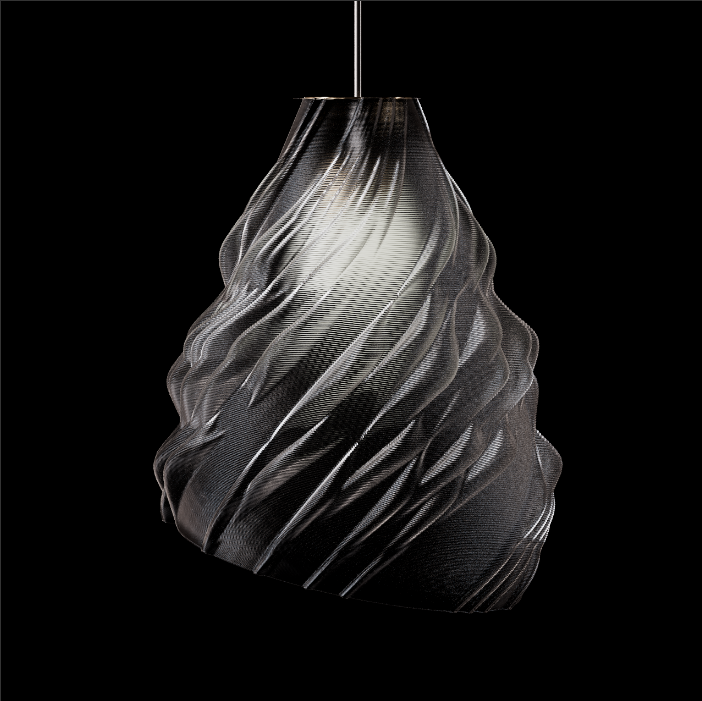
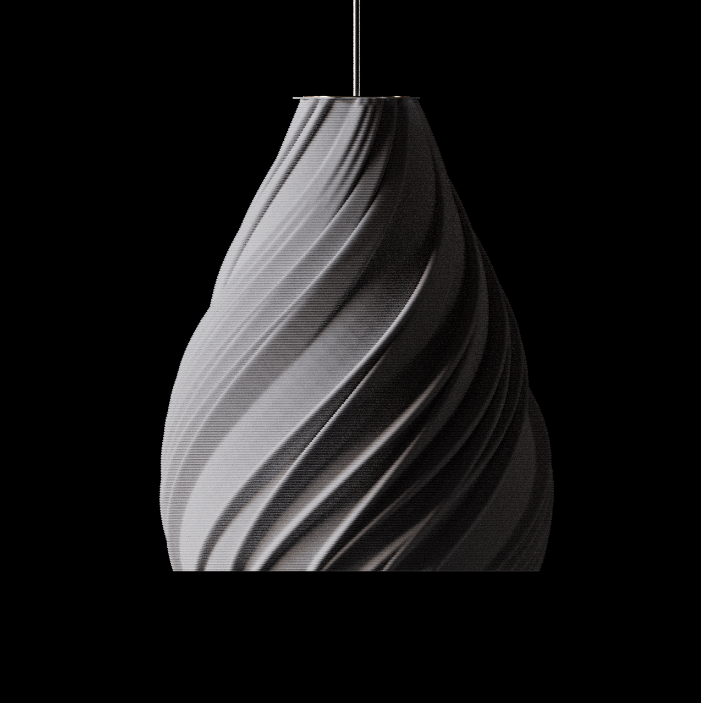
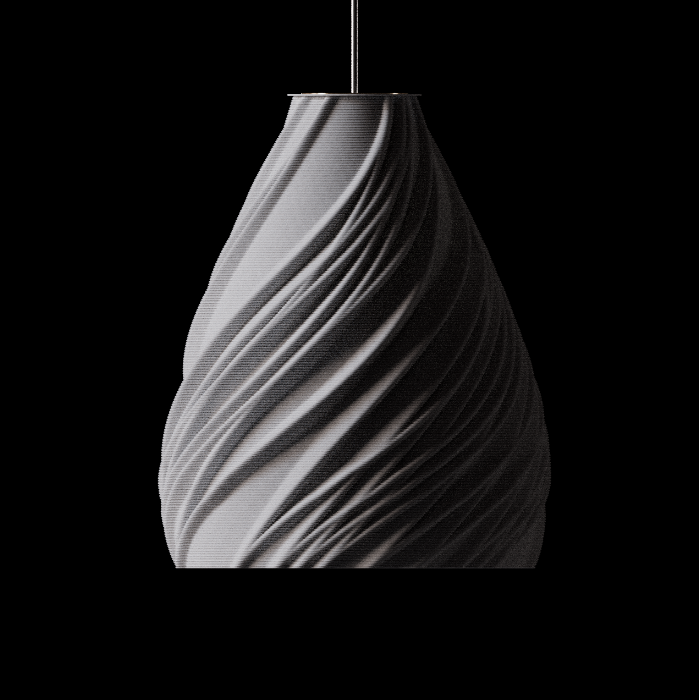

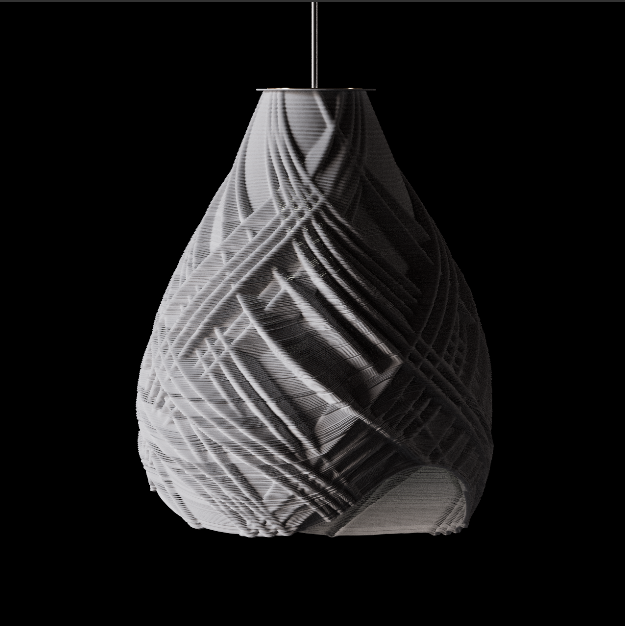
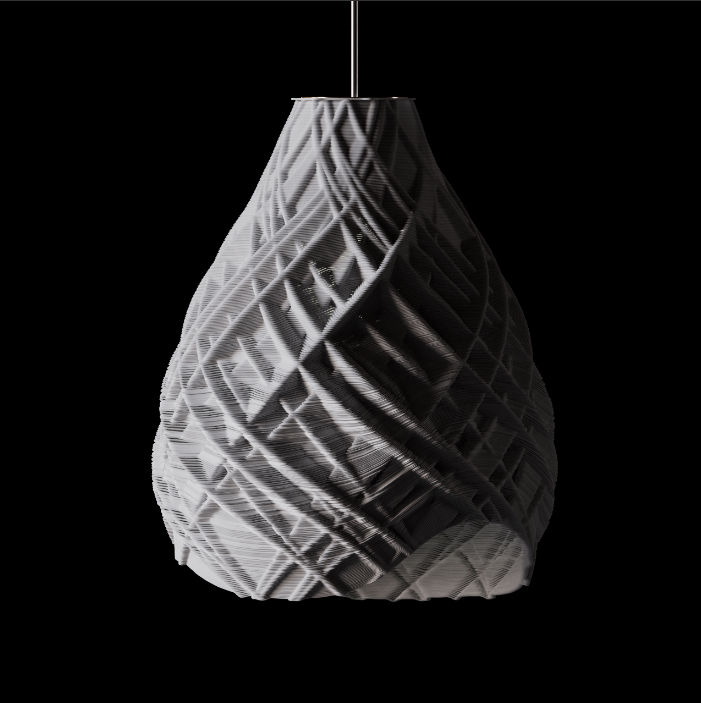
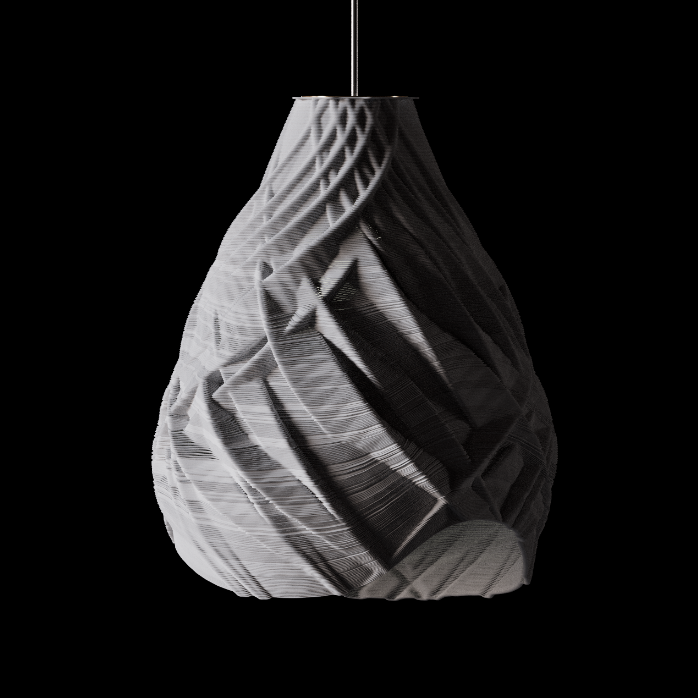
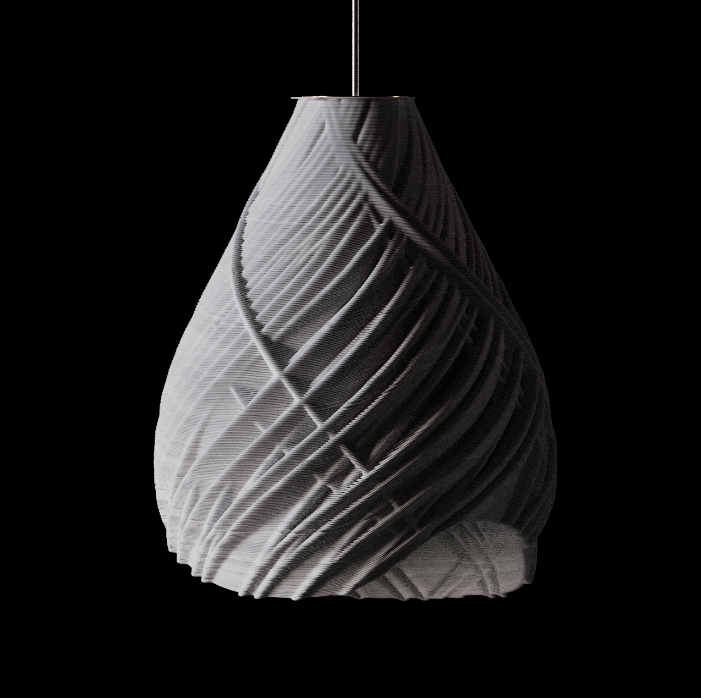
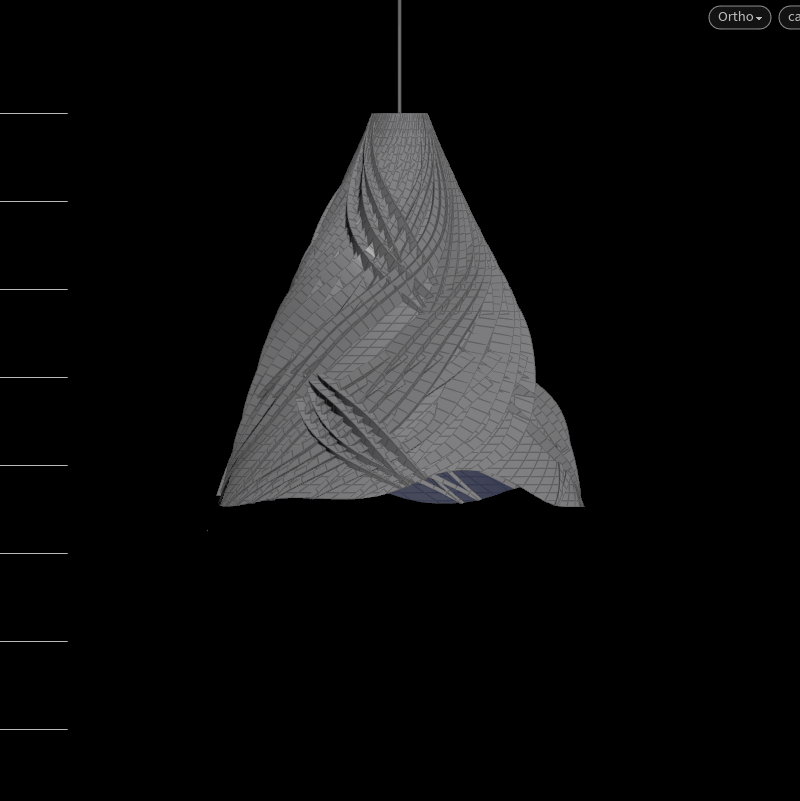
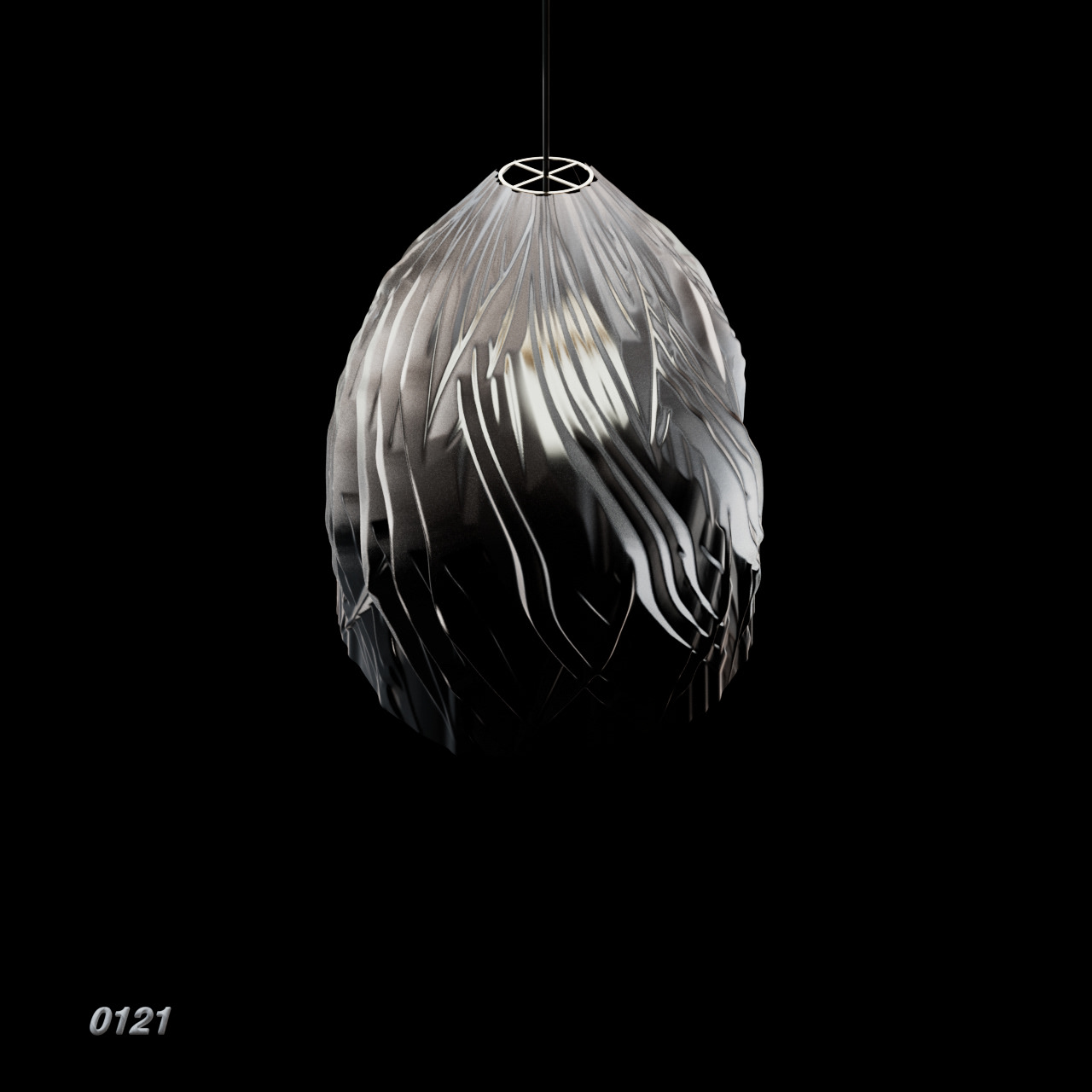
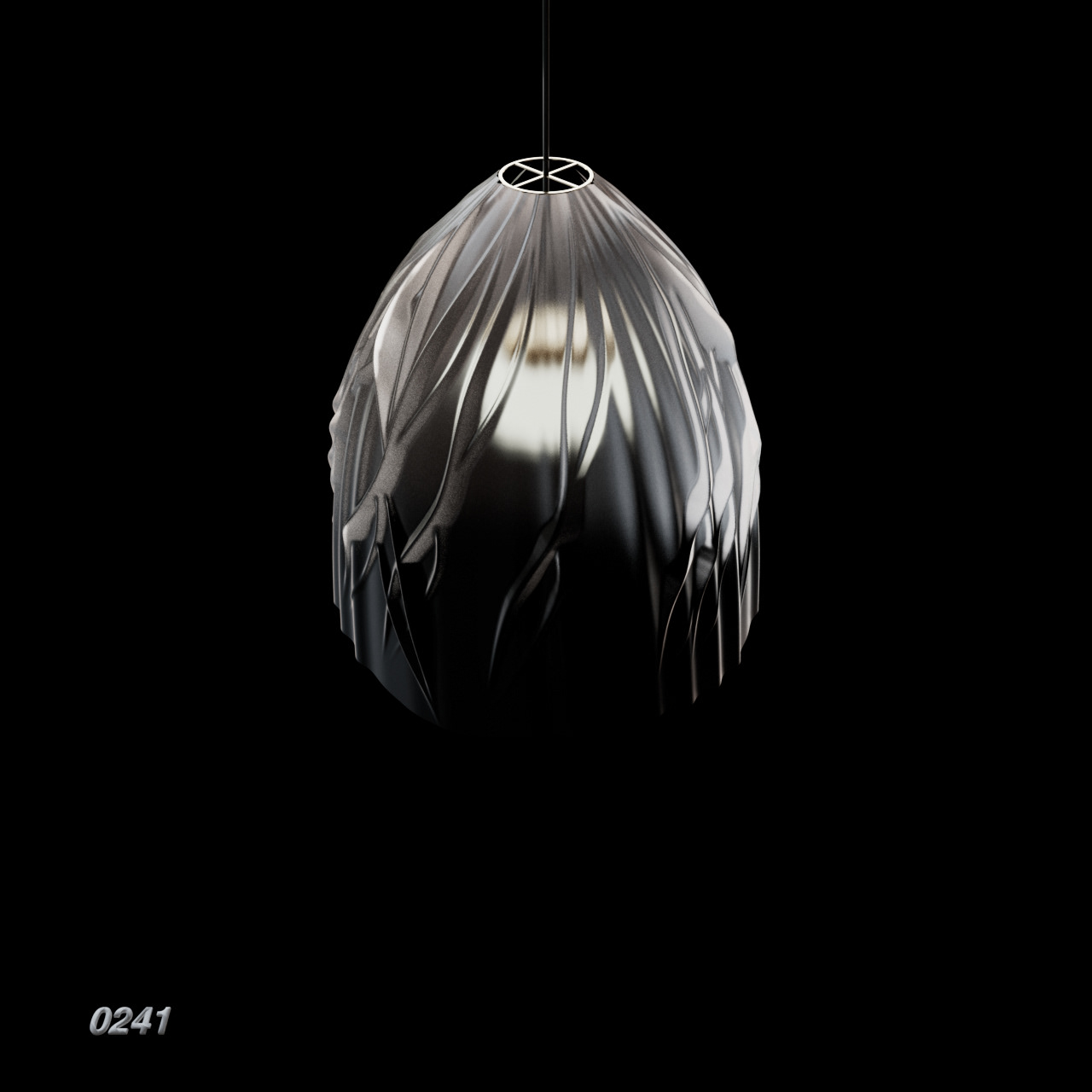
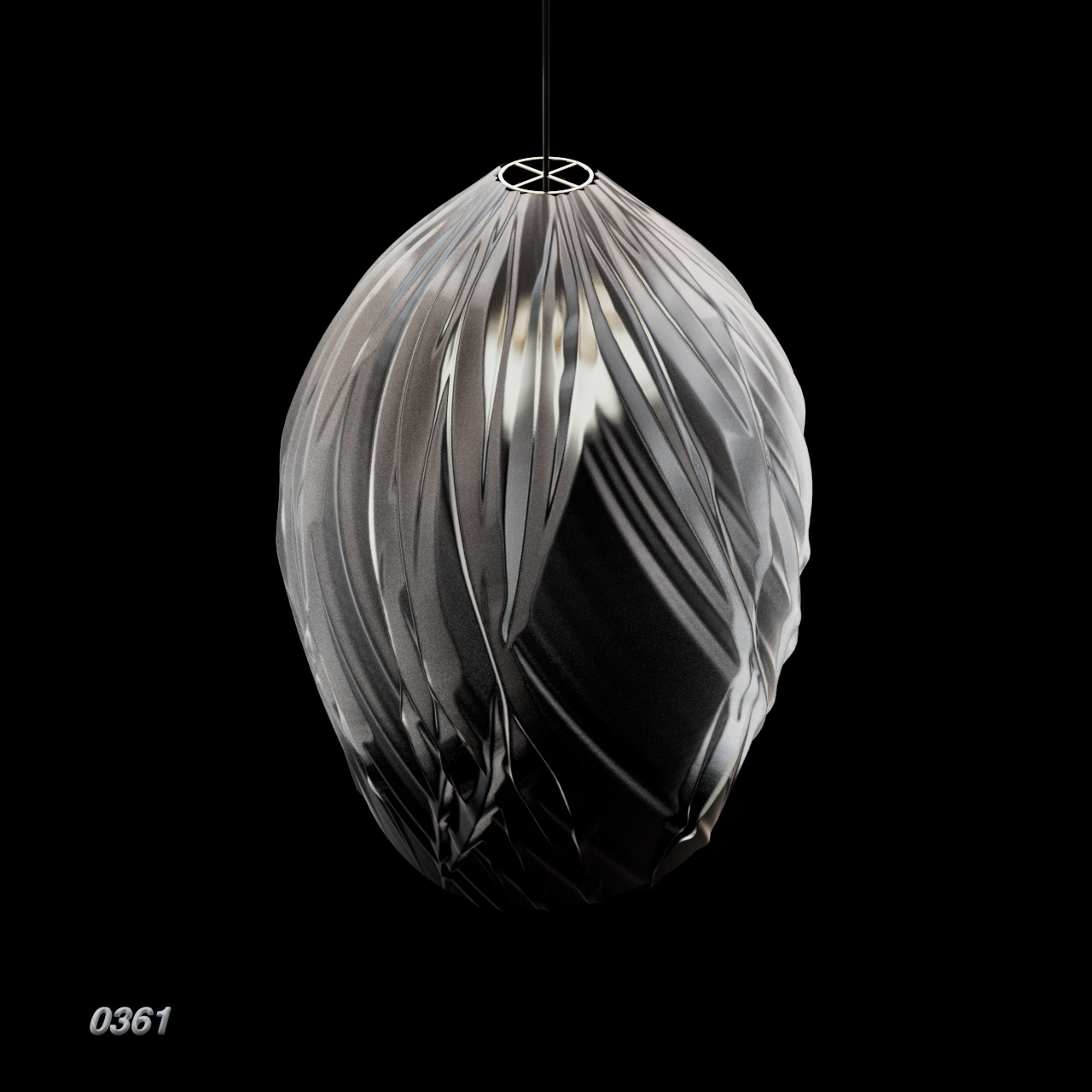
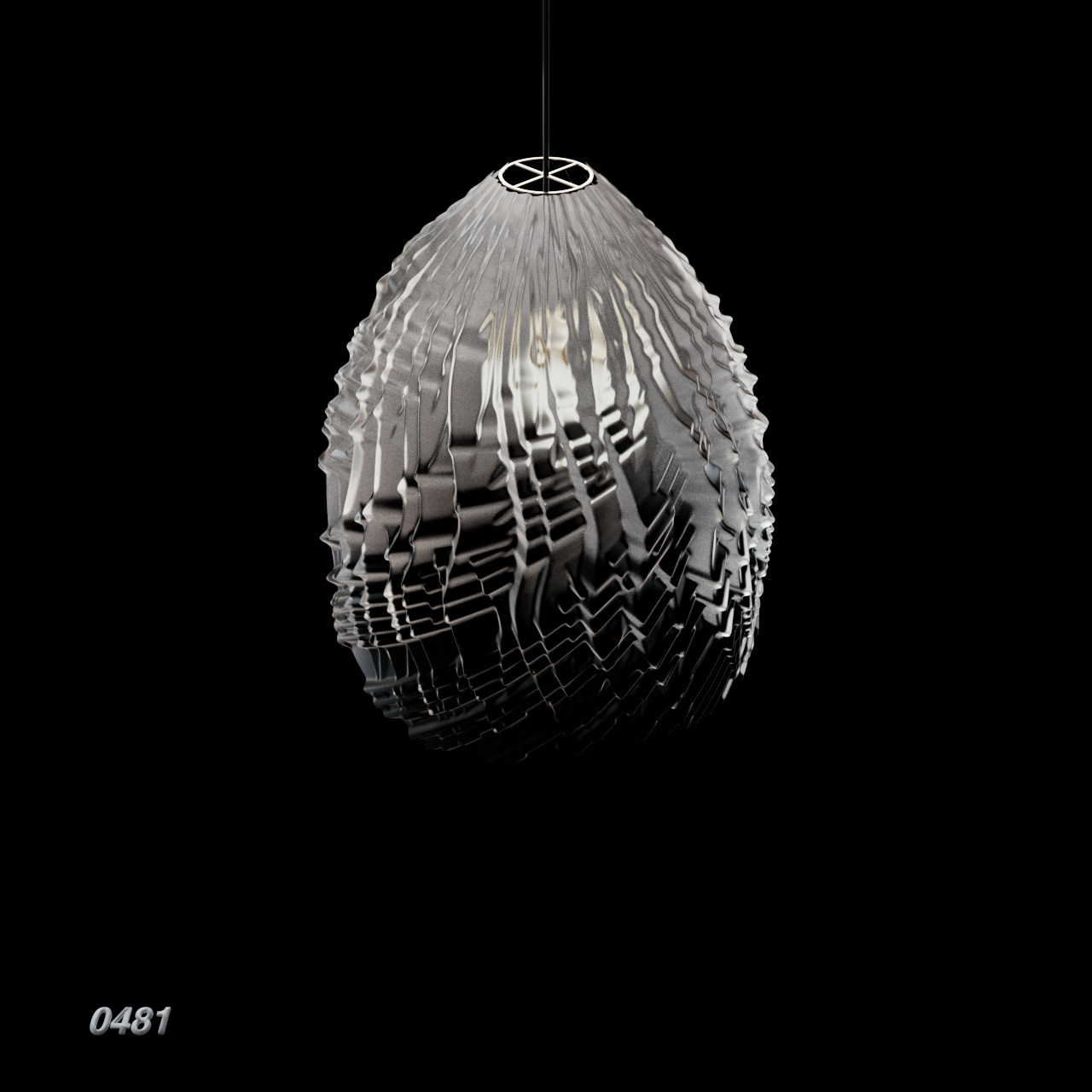

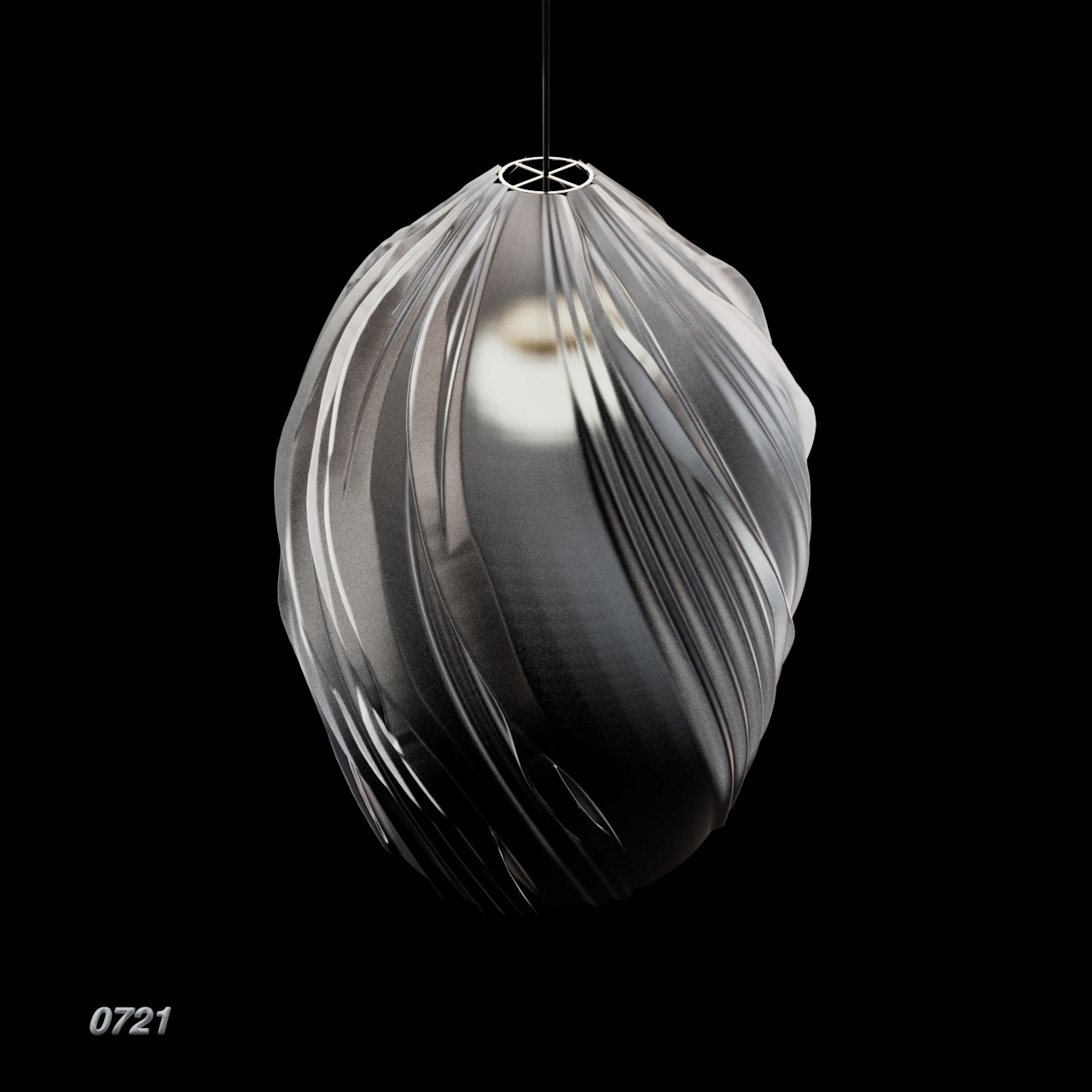
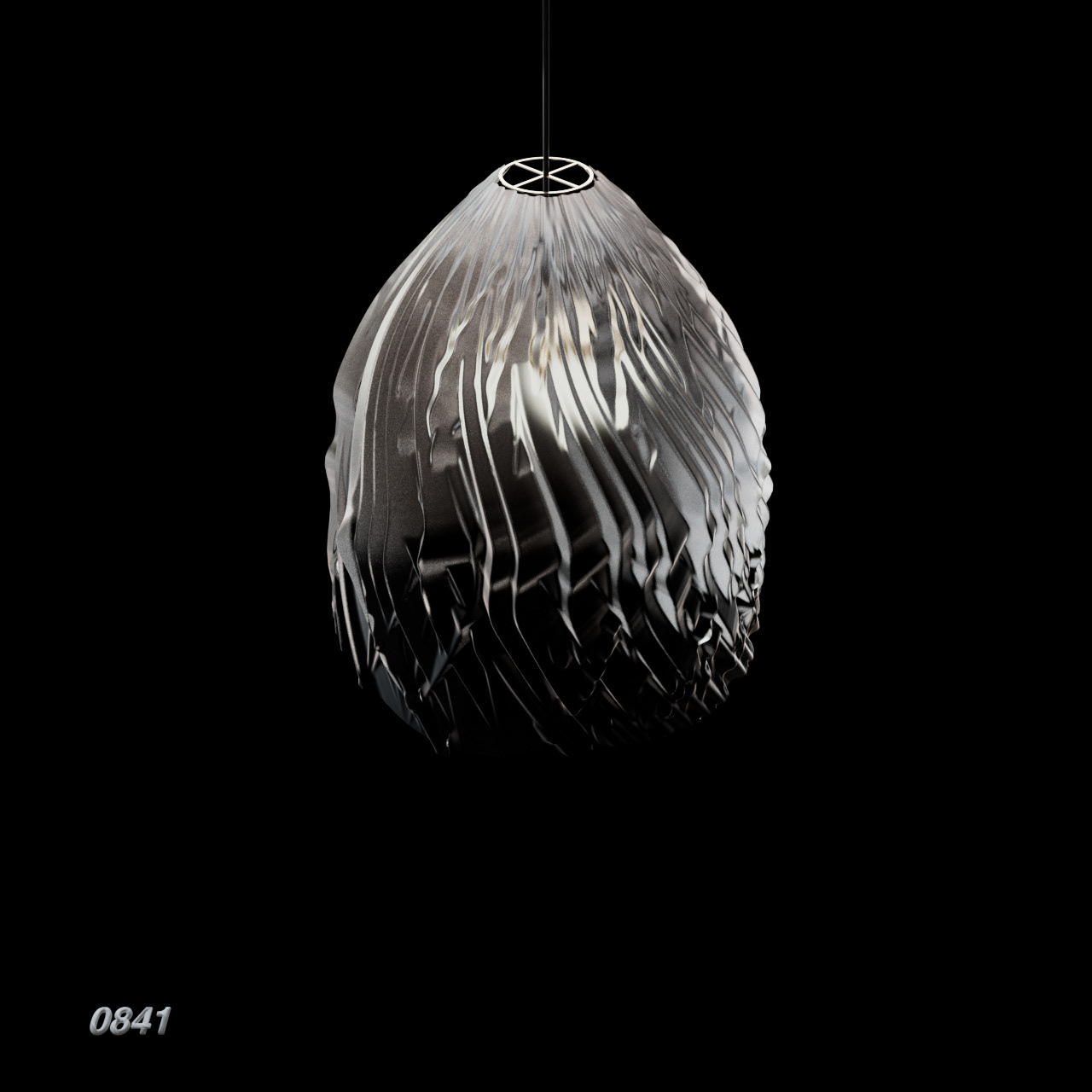
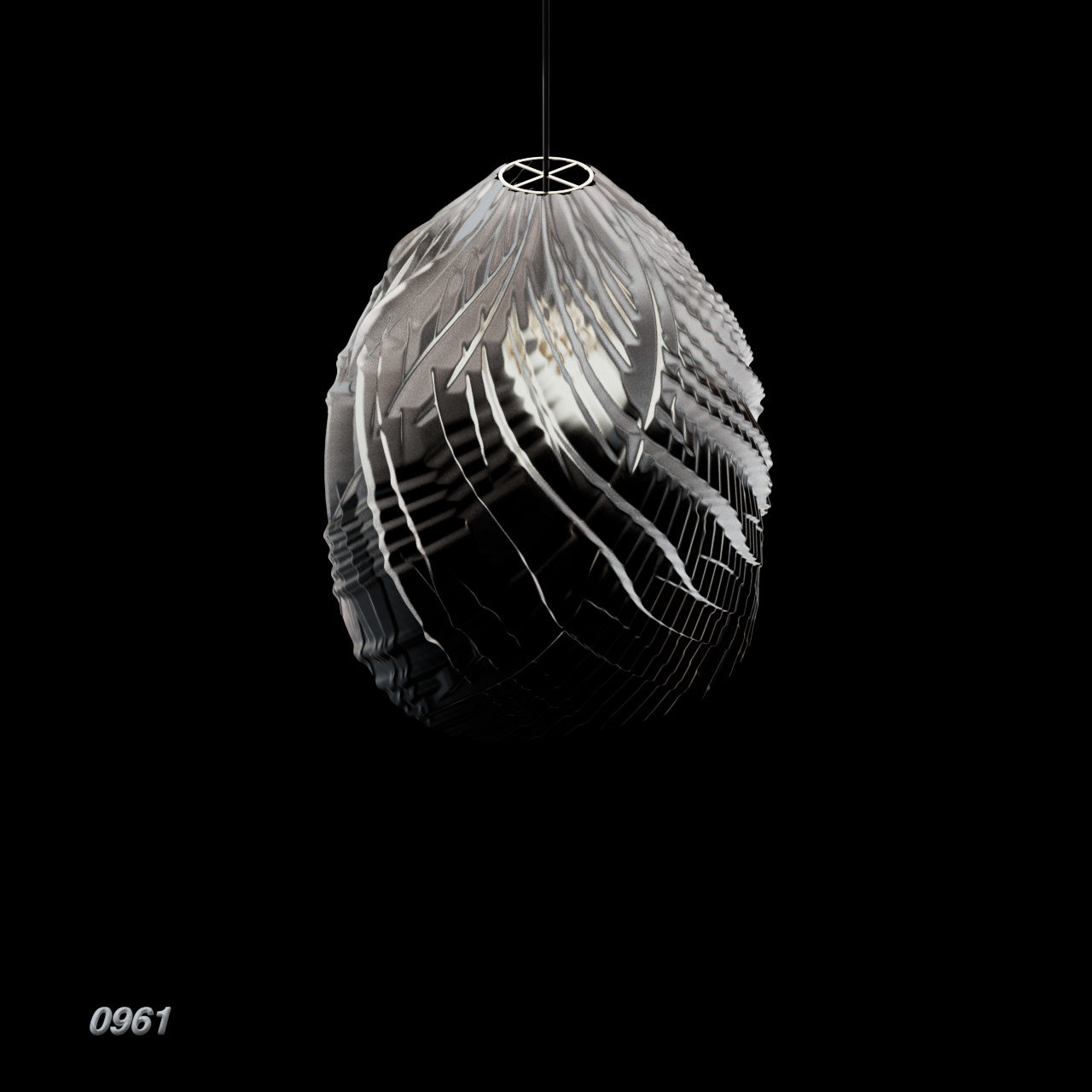
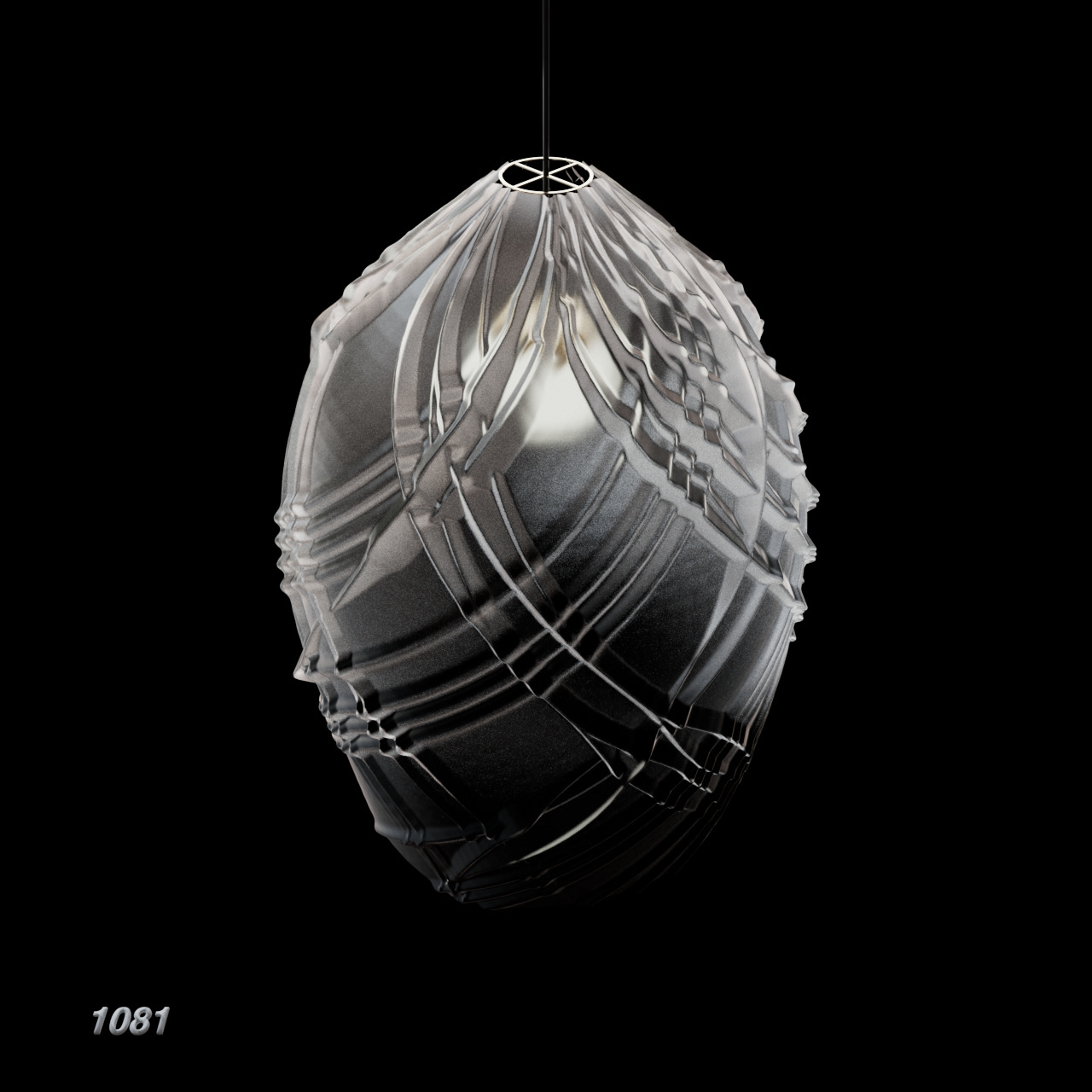